Albuskjell 1/6 A
- Installert i 1976
- Produksjonsstart 26. mai 1979
- Produksjonsstans 26. august 1998
- Fjernet i løpet av 2007 til 2013
- Også kalt «Albuskjell Alpha» eller «Albuskjell Alfa»

Albuskjell, som ligger 21 km vest for Ekofisk-senteret, er et gasskondensat-felt som strekker seg over to blokker, 1/6 og 2/4. Norske Shell fikk produksjonstillatelsen for blokk 1/6, mens Phillipsgruppen fikk tillatelsen for blokk 2/4. Feltet ble slått sammen med eierforholdet 50/50. Albuskjell ble oppdaget i 1972 da Norske Shell boret letebrønn 1/6-1X like ved grensen ved blokk 2/4. Phillips-gruppen og Norske Shell gikk sammen om boringen av denne brønnen.
Dannelsen av Albuskjell-strukturen skjedde noe ulikt dannelsen av andre felt i Ekofisk-området. Strukturen ble dannet for 22-55 millioner år siden over en saltkuppel. Det produserende laget på Albuskjell-feltet består av kalk med noe tynn skifer.
Plattformen Albuskjell 1/6 A produserte fra 11 brønner og var tilkoblet Ekofisk 2/4 R via Albuskjell 2/4 F gjennom en gass- og en oljerørledning. Et separat flammetårn var koblet til plattformen via gangbro. Prosessanlegget om bord bestod av separasjonsanlegg for olje og gass. Gassen ble deretter tørket og komprimert før den ble eksportert i en 24 tommer tykk rørledning. Oljen som ble separert ut, ble eksportert gjennom en 18 tommer tykk rørledning. Før gass og olje ble sendt inn i rørledningene, gikk de gjennom en fiskal målestasjon som målte mengden av gass og olje som ble produsert.
Plattformen ble konstruert i samarbeid mellom Cork Shipyard, OIS, Nylands Verksted, Tangen Verft, Aker Stord og Thyssen. Borekontraktør var Morco A/S. Understellet til begge Albuskjell-plattformene, var spesielt i og med at de to øverste rammene i understellet var fylt med vann slik at de ikke skulle kunne varmes opp i tilfelle brann. Understellet ble bygget ved Aker Verdal, mens dekket ble bygget ved Aker Stord.
Boligkvarteret hadde en kapasitet på 46 personer, senere 96 personer.
Vanndybden er 70 meter.
Total vekt på plattform og rørledninger var 25,300 tonn
Total høyde på flammetårnet var 94 meter over havet.
Total høyde på boretårnet var 74 meter.
Plattformen var opprinnelig konstruert som en kombinert bore-, produksjons- og boligplattform. I 1983 ble boligkvarteret med helikopterdekk skiftet ut og kapasiteten øket fra 46 til 96 personer. Selve løfteoperasjonen ble foretatt av kranlekteren «Balder» fra Heerema Seaways.
Frem til Albuskjell-feltet ble stengt i juli 1998 hadde det produsert:
7,353865 mill. Sm3 olje (millioner standard kubikkmeter)
15,53439 mrd. Sm3 gass (milliarder standard kubikkmeter)
0,990139 mill. tonn NGL (Natural Gas Liquids)
24,89468 mill. Sm3 o.e. (olje-ekvivalenter)
Brønnhoder
Etter at boringen av en brønn er ferdig, klargjøres brønnen for videre bruk. En brønn kan enten være en produksjons- eller en injeksjonsbrønn og vil derfor bli ferdigstilt, eller komplettert, etter behov og ønsket funksjon. Formålet med brønnkompletteringen er å isolere produksjonsstrømmen av olje og gass slik at det er mulig å ha en tett forbindelse fra reservoaret og helt opp til plattformen. Dette oppnås ved å montere foringsrør og produksjonsrør ned til reservoaret. Disse rørene festes i brønnhodet på plattformen.
Brønnhodene lukker toppen av foringsrørene og utgjør et system for kontroll av trykket i foringsrørene. På grunn av reservoartrykket strømmer råolje/gass opp gjennom produksjonsrøret til brønnhodet. I brønnhodet sitter det en hovedventil og en strupeventil. Disse gjør det mulig å stenge av en brønn eller å justere den ønskede produksjonsmengden fra hver brønn. På brønnhodet er det montert et ventiltre som inneholder kontroll- og arbeidsventiler. I ventiltreet sitter blant annet arbeidsvingventilen som gjør det mulig å injisere diesel og ulike kjemikalier inn i produksjonsrøret. Brønnhodet og ventiltreet er en del av brønnkontrollsystemet.
Hovedventilen sitter i den vertikale delen av brønnhodet. Den automatiske hovedventilen blir holdt åpen ved hjelp av hydraulisk trykk. Den støttes opp av den manuelle hovedventilen og er den første avstengningsventilen i brønnhodet.
Strupeventilen (Choke Valve) er konstruert for å kunne tåle et betydelig trykkfall og brukes til å regulere strøm og trykk av olje og gass. Strupeventilen regulerer strømmen fra de enkelte brønnene slik at trykk og produksjonsrate er tilnærmet lik fra alle brønnene. Produksjonen som strømmer gjennom strupeventilen føres til produksjons- og testsamleledningen gjennom en blokkventil. Olje-/gass-strømmen blir deretter ført til separatoren på plattformen.



Separasjon
Produksjonsbrønnhodene leverer en blanding av råolje og naturgass til separatorene enten gjennom samleledningene for produksjon eller test. Blandingen av gass, olje og vann fra brønnene må separeres for videre behandling på plattformen.
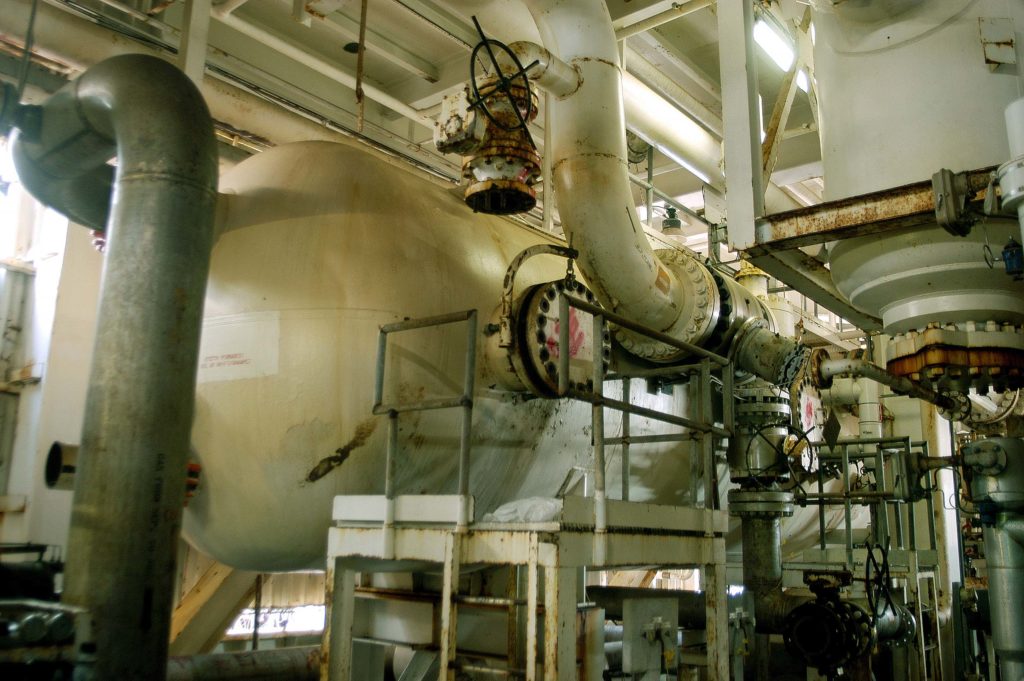
Produksjonsseparatoren er en 20 meter lang horisontal tank som er 4 meter i diameter. Den arbeider ut fra prinsippet om at den tyngste væsken i tanken synker ned på bunnen og lettere væsker og gass ligger over denne. Det er en 3-faseseparator med en nedre fase av vann, en midtre fase av råolje og en øvre fase av gass. Innvendig er den utstyrt med innløpsavbøyer, sju perforerte ledeplater og en dråpefanger for gassutløpet.
Testseparatoren arbeider etter samme prinsipp som produksjonsseparatoren, men er noe mindre. Den brukes til å teste blant annet produksjonsrate fra en enkelt brønn slik at strupeventilen i brønnhodet kan justeres riktig.
Gasskompresjon
Kompresjonsprosessen var nødvendig for å øke trykket før gassen kunne sendes inn i rørledningen til Ekofisk 2/4 R. Kompresjonsenheten besto av gasskjøler, væskeutskiller og kompressor.
Gasskjøler: Hensikten med gasskjøleren er å senke temperaturen på gassen fra separatoren. Dette må gjøres for at kompressoren ikke skal gå for varm. Gasskjølere inneholder flere vannkjølte rør som gassen sirkulerer rundt. Gassen har 27°C etter avkjøling.
Væskeutskiller: Når temperaturen på gassen senkes, vil noe væske utskilles. Denne må fjernes i væskeutskilleren (suction scrubber) som er en vertikal tank 4 meter høy og 2 meter i diameter.
Gasskompressor: Kompressoren, som er drevet av en gassturbin, øker trykket fra 465 psig til 1305 psig. Samtidig øker temperaturen på gassen fra 27°C til 100°C.
Gasstørking
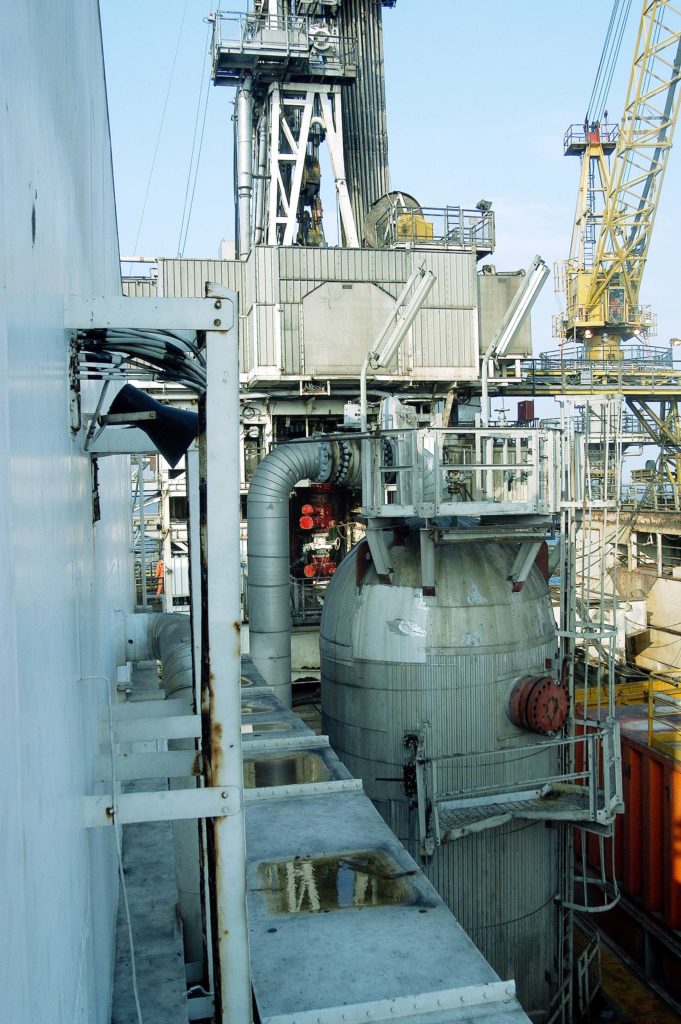
Gassen som ble eksportert i gassrørledningen til Ekofisk 2/4 R måtte være helt tørr, ellers kunne is og hydratpropper danne seg i rørledningen under transporten gjennom det kalde sjøvannet.
Først kjøles gassen ned fra 100°C til 27°C i to steg før den mikses med en væske som trekker til seg vannet (trietylenglykol). Etter at gassen har vært i kontakt med glykol og blitt tørket, blir den igjen varmet opp til 65°C i en varmeveksler.
Gasstørkesystemet består av gass/gass varmeveksler, gasskjøler (etterkjøler) og tørkeenhet (Glycol Contactor).
Gass/gass varmeveksler: Varmeveksleren har to funksjoner; å kjøle den innkommende gassen (100 – 60°C) og varme opp den utgående gassen (27 – 65°C). To gasstrømmer passerer hverandre i denne varmeveksleren.
Gasskjøler (etterkjøler): Gasskjøleren inneholder flere vannkjølte rør som gassen sirkulerer rundt (60°C – 27°C).
Tørkeenhet (Glycol Contactor): Tørkeenheten er en vertikal tank som er 13 meter høy og 2 meter i diameter. Gassen bobler opp gjennom en rekke kar fylt med glykol og ender opp på toppen av tanken som tørr gass. Glykol som er mettet med vann sirkuleres ut og ny tørr glykol pumpes inn.
Etter igjen å ha passert gass/gass varmeveksleren holder gassen en temperatur på 65 °C. Gassen er nå helt tørr og klar for eksport.
Fiskale målesystemer
Olje og gass som produseres på plattformen og eksporteres til Ekofisk-senteret måles i en målestasjon på plattformen. Data fra disse instrumentene ble sendt til en datamaskin (Daniel Computor) for prosessering før signalene ble sendt til Ekofisk-senteret via en telemetri link.
Det var også tilsvarende måleenheter for gass som ble brukt på plattformen og for flammetårnet.
Gassmåling: Gassmåleren består av et rør som inneholder en trykkmåler, en temperaturmåler, en tetthetsmåler og en restriksjon (flow orifice). Gasstrømmen blir ført gjennom en restriksjon i gasslinjen. Når gassen passerer denne restriksjonen øker hastigheten på gassen og samtidig faller trykket. Utfra kjennskap til gassens tetthet og komposisjon vil en da kunne bruke dette trykkfallet til å måle mengden nøyaktig.
Oljemåling: For å måle oljen blir et turbinmeter brukt. I ytterkanten av rotoren sitter det små magneter som gir signaler til følere i rotorhuset. Disse følerne kan da måle hastigheten rotoren går rundt med, og utfra dette måle nøyaktig hvor mye væske som går gjennom måleren.
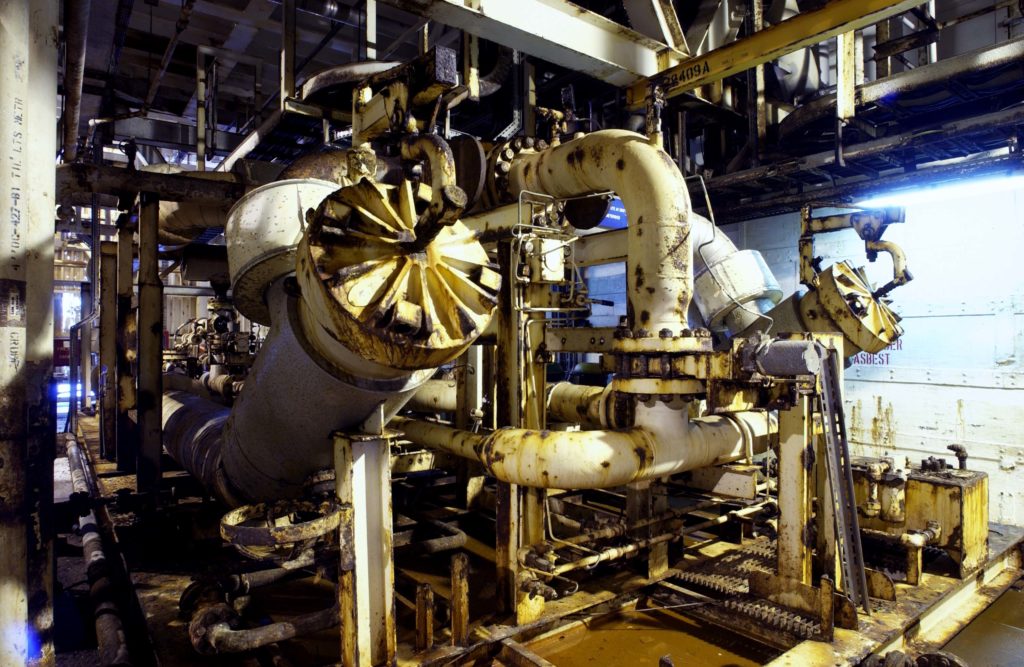
Kalibrering: Det vil være nødvendig å kalibrere et slikt turbinmeter jevnlig for å sikre gode målinger. Kalibratoren (Meter Prover) består av en hesteskolignende prøvesløyfe. Inne i denne sløyfen er det en gummiball. Under kalibreringen blir olje ført inn i prøvesløyfen og skyver gummiballen foran seg. Ved å måle tiden det tar for gummiballen å gå rundt sløyfen samt at en kjenner sløyfens nøyaktige volum, vil en kunne måle oljestrømmen nøyaktig. Disse data blir så sammenlignet med pulsene fra turbinmeteret.
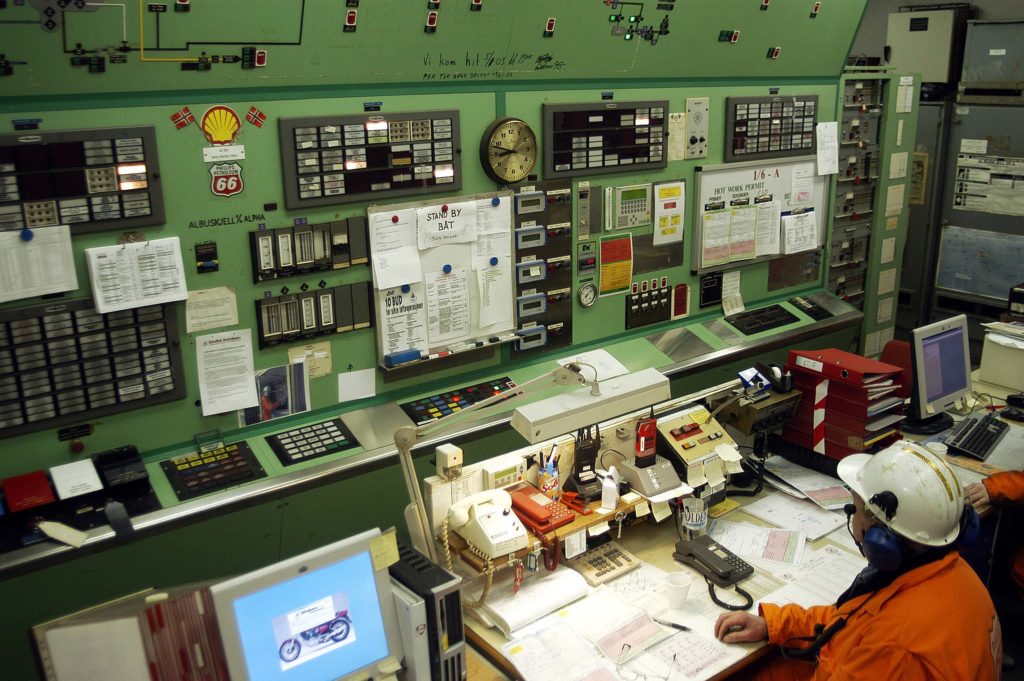
Kontrollrom
Kontrollrommet er plattformens hjerte. Herfra overvåkes og styres alle viktige prosesser på plattformen.
Hjelpesystemer
Glykol regenerering: Glykol fra gasstørkeren har et trykk på 1205 psig og er mettet med vann og gass. Først blir trykket redusert før gassen fjernes i en avgasser (Degassing Pot). Glykolen blir så filtrert og varmet opp i regeneratoren hvor vannet fordamper. Den tørre glykolen går deretter gjennom pumper for å få samme trykket som gasstørkeren der den igjen blir injisert.
Pigging
Gassrørpigging: For å fjerne slagg og vann i gassrørledningen ble det sendt en rund ball inn i gassrøret på Albuskjell 1/6 A. Denne fulgte med gasstrømmen til Ekofisk der den ble fjernet.
Oljerørpigging: Rørskrapen i oljeledningen har en annen form enn gassrørskrapen, men fungerer ellers på samme måte.


Andre hjelpesystemer
Kraftforsyning: Den elektriske kraften til plattformen ble produsert i generatorrommet. Fire elektriske generatorer var hver drevet av en Kongsberg gassturbin. Senere ble to av turbinene fjernet og en dieselmotor installert. De elektriske tavlene var plassert i modulen over generatorene. Arbeidsspenningen var 480 volt.
Andre hjelpesystemer på plattformen var: Brannsystemer, redningsutstyr, instrumentluft, injeksjon av kjemikalier, drikkevann, diesel og smøreolje, gassløftutstyr, verksted, helikopterdekk, boligmodul, flammetårn, radiokommunikasjon og så videre.
Produksjonen opphørte i 1998 og i 1999 ble plattformen fraflyttet og fjernovervåket fra Ekofisk 2/4 K. Prosessanlegget ble rengjort og brønnene plugget og sikret. Plattformen ble fjernet i løpet av 2013.





