Offshore engineering department

Most of the supporting engineers, geologists and so forth are located at the head office in Tananger. Metering and lab staff helped to keep track of the oil and gas produced and its quality, while the production control team coordinated output.
Production control
The offshore production control unit (PCU) reported to the technical manager, but worked closely with its counterpart on land. Two people worked the day shift and one at night.
They did long-term planning, followed up metering activities, coordinated production, compiled daily output reports and received all the analyses from the laboratory.
Other duties include checking results from the metering stations, testing production quality and checking that the Emden terminal received enough gas to meet demand from European buyers.
In the event of a shutdown, the PCU had to carry out a “linepack” – in other words, calculate how long gas deliveries could be maintained by the volume already in the pipeline.
If gas output from Ekofisk failed to meet the amount ordered, the shortfall had to be made good by buying from competing suppliers.
During the early years, the PCU was a one-man show. Its work increased, however, and staffing was doubled to two people from 1980.
They were still only on the day shift, but round-the-clock staffing became necessary from 1985 when a third person was added. This function is run from land today.
Metering group
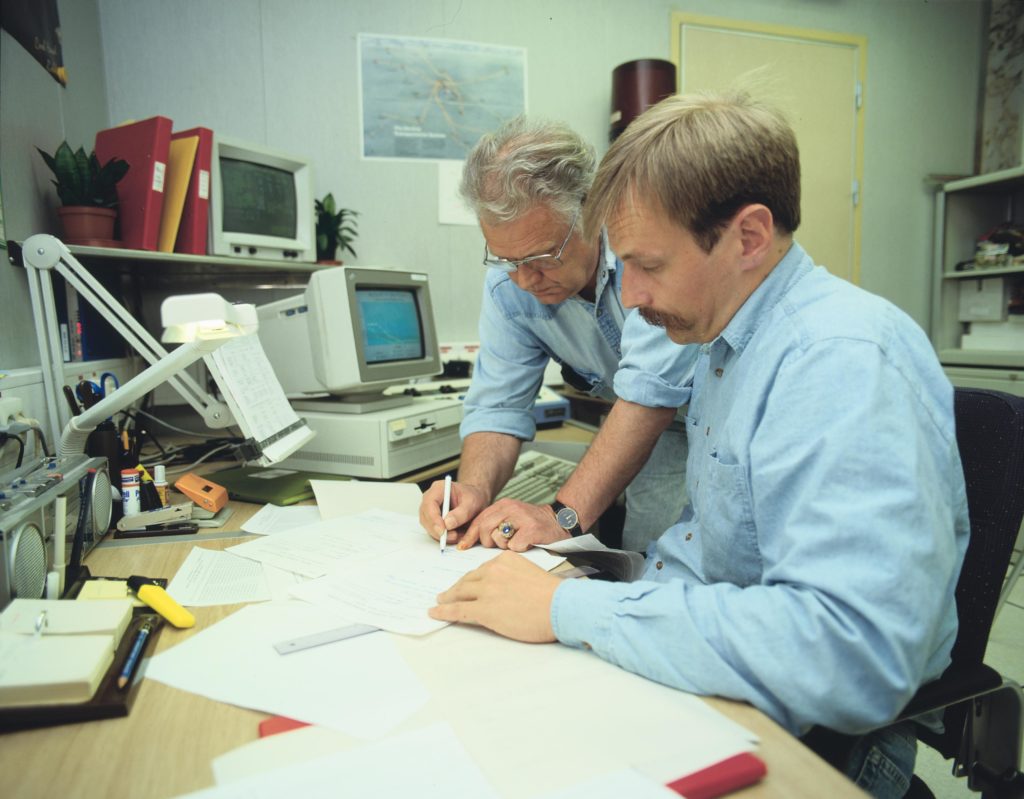
This team was responsible for allocation metering – measuring what was being produced and where. Once these data had been compiled, they were sent to the production control unit (PCU).
The information was required because oil and gas composition as well as licensee holdings varied between the Greater Ekofisk Area fields.
That made it important to have an overview of how much was produced in the various grades from the different fields at any given time.
With the PCU, the metering group calculated the shares of each partner. It was staffed by people with expertise as automation and instrumentation engineers or technicians.
Laboratory personnel
Lab staff have qualifications as chemical and process engineers or technicians, and are responsible for allocation and processing analyses. This means they determine the composition of the various production streams.
Samples are taken from the gas being piped to Emden, for example. This flow is broken down into its various components to establish its make-up.
Similarly, crude samples are distilled into three components – gas, light oil and heavy oil. The oils produced from the various fields look different. Cod crude is very pale, for example, while output from Valhall is completely black.
The lab analyses are significant for the price fetched by the various petroleum types, as well as for ensuring that their processing is optimal.
A number of parameters also have to be followed up through these process checks, including composition, density, water content, dew point and oil in water.
Lab staff also examine samples to ensure that emissions to the air and discharges to the water remain within the legal limits. The Norwegian Environment Agency gets continuous reports on this.
Other samples are taken from the coolant water system, and from the glycol used to dewater the gas.
The lab team used to be based on the Ekofisk tank and totalled 17 members. Many measurements can now be followed up online, however, so offshore staffing has been cut to one person on 2/4 H in the Ekofisk Complex and another in the Eldfisk Complex.
Reservoir engineers
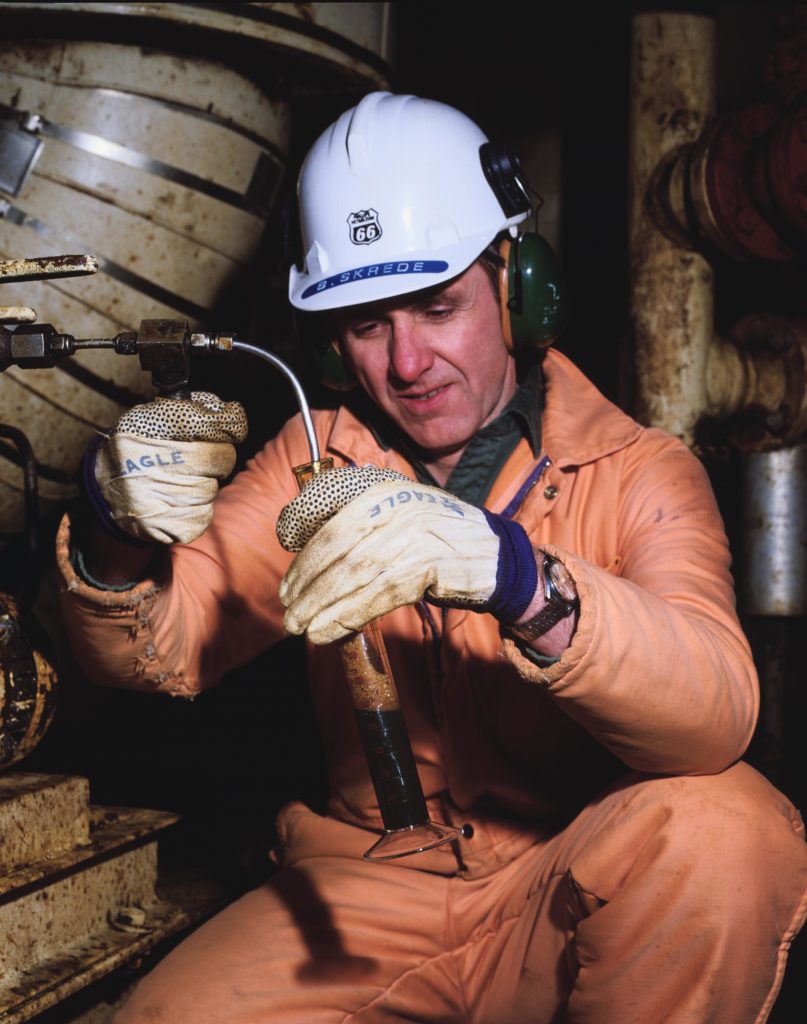
Most of Ekofisk’s reservoir engineers work on land today. In the 1970s, however, it was normal for some to be stationed permanently at the Ekofisk Complex.
After an oil and gas field has been discovered and studied by the geologists, reservoir engineers start to analyse whether it can be produced in both technical and commercial terms.
They must determine what resources the sub-surface structures contain, and how they will behave as their content is depleted by production.
The reservoir engineer’s most important task is to interpret wells on the basis of logs and with the aid of various parameters. They must be able to evaluate reservoir properties, including the identification of porous and permeable zones, in order to plan optimal recovery.
Modern computer-based tools are used today for acquiring and interpreting well information, and a range of data types gets integrated in this work.
The gamma log registers natural gamma radiation from the rocks, making it possible to distinguish between sandstone, carbonates and shales.
Neutron lifetime measurements provide some indication of water saturation behind the well casing, while sonic logs specify how fast sound travels through the rocks and indicates their porosity.
In addition, resistivity logging measures whether rock pores contain oil or gas, while density logs register how dense the rocks are.
Interpreting these data utilises sophisticated computer hardware and the best-available and most advanced software. The oil industry has some of the world’s top computer tools.
With this equipment, advanced three-dimensional models of a reservoir are constructed by the specialists in order to calculate its life cycle.
Much of the work is done in teams and in collaboration with other departments and specialists. Reservoir engineers are involved throughout the useful life of a petroleum field from its development stage.