Edda 2/7 C
- Installed 1976
- On stream 2 December 1979
- Shut down 1998
- Removed in 2011-12
- Also known as Edda Charlie

This oil and gas reservoir lies 12 kilometres south-west of the Ekofisk Complex. The exploration wells were drilled from Ocean Viking and Zapata Nordic in 1972 and 1973.
Edda 2/7 C was originally designed as a combined production, drilling and accommodation platform with a separate flare stack and two submarine pipelines to Ekofisk 2/4 R. However, the drilling rig was transferred in 1987 to Ekofisk 2/4 K and a new process module was installed the following year to handle production from Tommeliten 11.8 kilometres to the west.
Although the platform had 15 well slots, only 10 of these were used. Its processing facilities comprised an oil/gas separator. The gas was compressed to boost its pressure and then dewatered before being piped through a 12-inch line to Ekofisk 2/4 R in the Ekofisk Complex.
After separation, the oil was pumped through a 10-inch line to 2/4 R. Before entering their respective pipelines, the oil and gas passed through a fiscal metering station which measured the volumes produced.
Living accommodation: 32 beds.
Water depth: 71 metres.
Cellar deck 19 metres above sea level.
Top of derrick 94 metres above sea level.
Production ceased in 1998, with the platform becoming unmanned the following year and remotely monitored from Ekofisk 2/4 K. Such monitoring included emergency shutdown, fire and gas systems, ventilation, power supply and well status. The processing plant was cleaned, the wells plugged and secured, and 2/7 C removed in 2011-12.
When the platform was shut down in July 1998, it had produced:
30 million barrels or 4.81731 million standard cubic metres (scm) of oil
1.97332 billion scm of gas
0.21107 million tonnes of natural gas liquids (NGL)
Wellheads
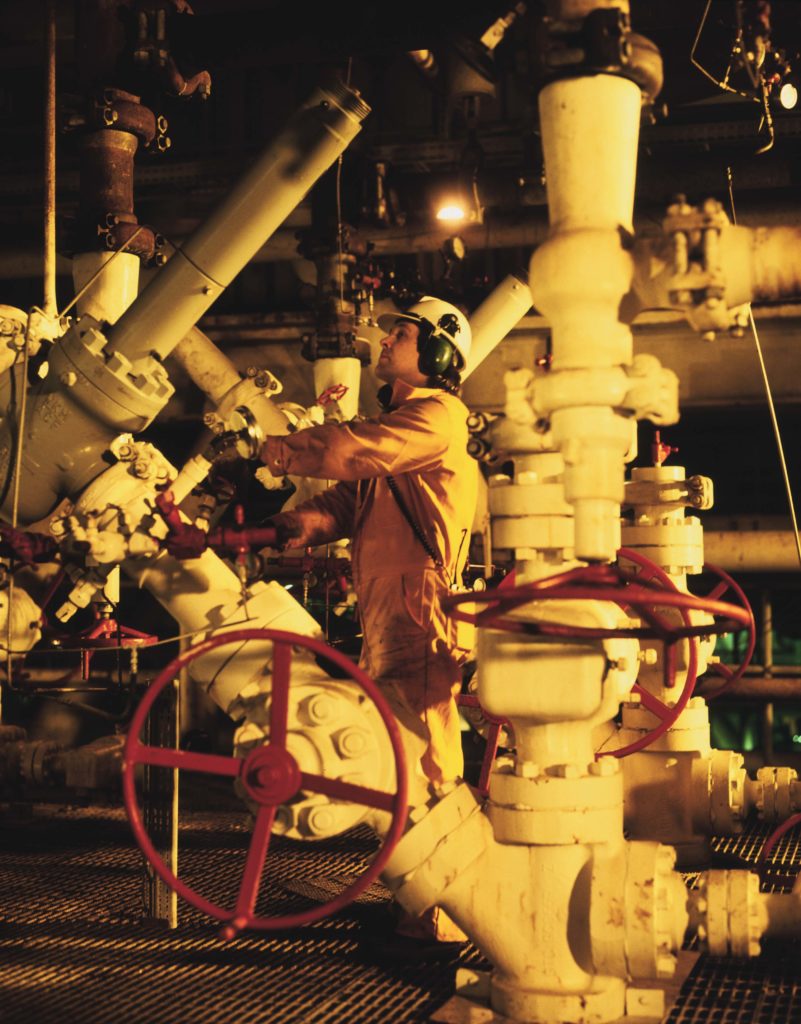
Once a well has been fully drilled, it is completed for either production or injection. The purpose of well completion is to isolate the oil/gas production flow (wellstream) so that the whole path from reservoir to platform topside is leak-free.
This is achieved by running production tubing inside the casing (well liner) installed during drilling. These tubes are attached to the wellhead on the platform, which seals the top of the casing and provides a system for controlling pressure in the well.
Reservoir pressure causes crude oil/gas to flow up through the production tubing to the wellhead, which contains master and choke valves. These make it possible to shut down a producer or to adjust the desired volume of flow from each producer.
The Xmas tree (so called because of its shape) is installed on the wellhead. It contains control and work valves, such as the one for injecting diesel oil and various chemicals into the production tubing. Wellhead and Xmas tree form part of well control system.
The automatic master valve sits in the vertical section of the wellhead and is kept open by hydraulic pressure. Supported by the manual master valve, it represents the first barrier for shutting down the well.
Designed to cope with a substantial pressure drop, the choke valve is used to regulate wellstream flow and pressure from the individual well. This ensures that pressures in and production rates from all the wells are virtually identical.
The wellstream flowing through the choke valve is conducted to the production or the test manifold through a block valve before entering the separator on the platform.
Separation
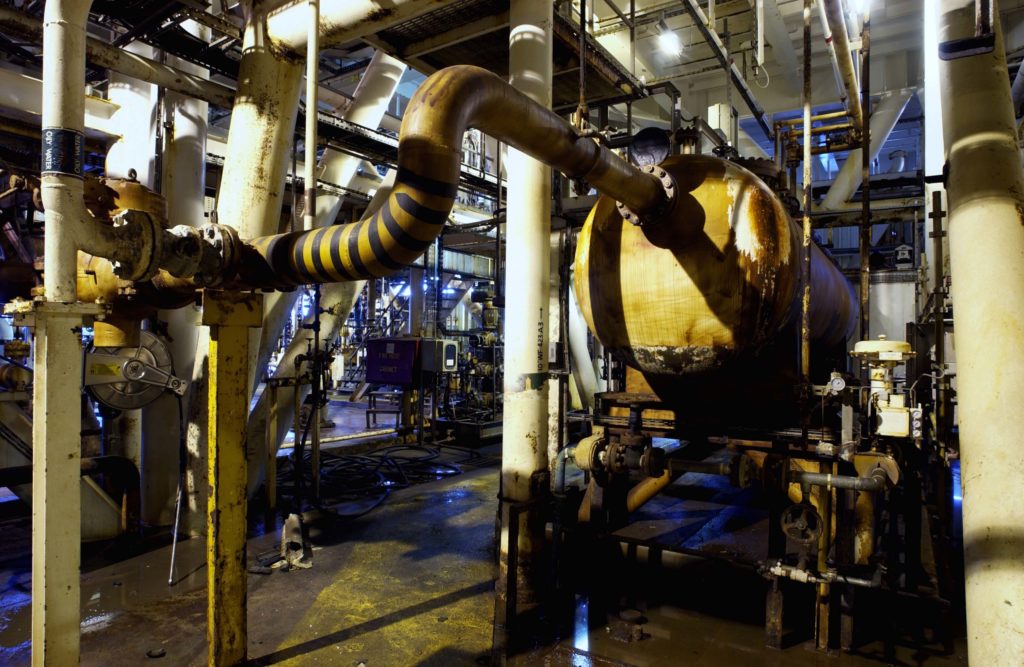
The wellheads delivered a mix of crude oil, natural gas and water through either the production or the test manifold to the separators. This mix had to be split into its various components for further processing on the platform.
Measuring 20 metres long, the production separator was a horizontal tank with a diameter of four metres. It worked on the principle that the heaviest components in the tank would sink to the bottom while the lighter liquids and gas remained higher up.
This was a three-phase device with a lower phase of water, a middle one of crude oil and an upper gas phase. It was equipped internally with inlet deflectors, seven perforated guide plates and a demister for the gas outlet.
The test separator worked on the same principle, but was rather smaller. Its applications included testing the production rate from a single well so that the choke in the wellhead could be correctly adjusted.
Gas compression
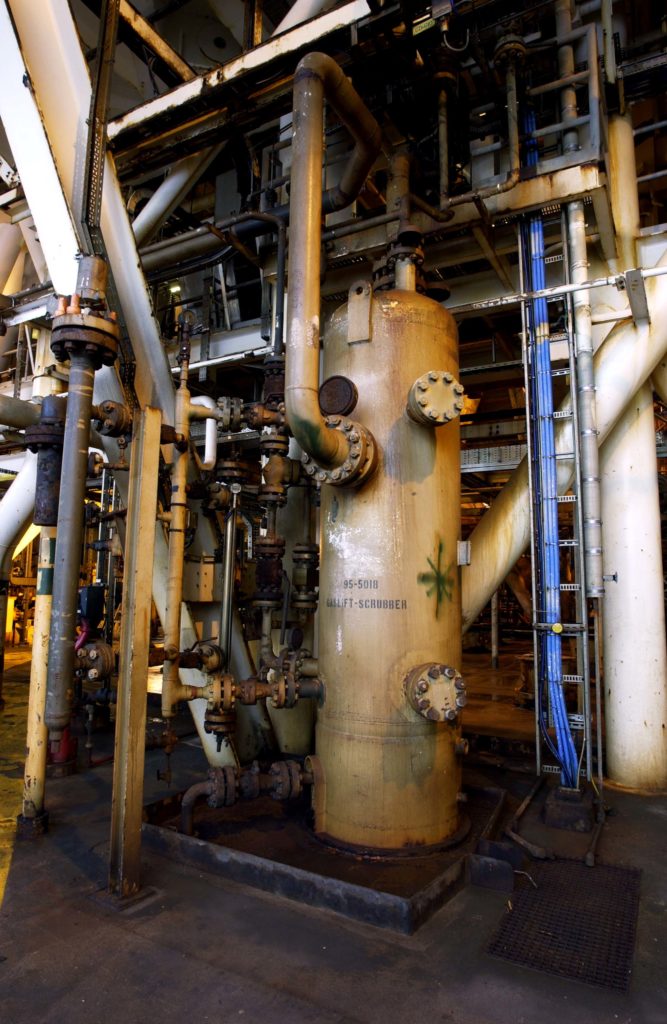
Compression was needed to increase the gas pressure before it entered the pipeline which ran to Ekofisk 2/4 R. The train comprised a gas cooler, suction scrubber and gas compressor.
Gas cooler. This reduced the temperature of gas emerging from the separator in order to prevent the compressor from running too hot. The gas circulated around a set of water-cooled tubes, lowering its temperature to 27°C.
Suction scrubber. Once the gas was cooled, some liquids had to be removed in this device. It comprised a vertical tank four metres tall and two metres in diameter.
Gas compressor. Driven by a gas turbine, this unit increased the pressure from 465 pounds per square inch gauge (psig) to 1 305psig while also raising the gas temperature from 27°C to 100°C.
Gas dehydration
Gas piped to Ekofisk 2/4 R had to be completely free of water to avoid ice or hydrate (hydrocarbon ice) plugs forming in the pipeline during transport through the cold seawater.
The gas was first cooled from 100°C to 27°C in two stages before being mixed with triethlyene glycol – a liquid which attracts water. After it had been dehydrated in this way, the gas was reheated to 65°C in a heat exchanger.
In all, the dehydration system comprised the gas/gas heat exchanger, the gas aftercooler and the glycol contactor.
Gas/gas heat exchanger. This had two functions – cooling down the incoming gas from 100°C to 60°C and heating up the outgoing gas from 27°C to 65°C. Two gas streams passed each other in the unit.
Gas aftercooler. This contained a number of water-cooled tubes which the gas circulated around to reduce the temperature from 60°C to 27°C.
Glycol contactor. This unit comprised a vertical tank 13 metres tall by two metres in diameter. The gas bubbled up through a number of vessel filled with glycol and ended up dehydrated at the top. Water-saturated glycol was circulated out and replaced by more dry chemical.



Fiscal metering
Oil and gas processed on the platform and exported to the Ekofisk Complex was metered in a metering station on 2/7 C. Data from these instruments were transmitted to a Daniel computer for processing before being transferred to the Ekofisk Complex via a telemetric link.
Corresponding meters were also provided for gas consumed on the platform and for the flare boom.
Gas metering. The gas meter comprised a tube containing pressure and temperature gauges, a densimeter and a flow orifice. When the gas passed through the orifice, its speed rose and its pressure fell. Knowing the density and composition of the gas meant the pressure drop could be used to measure the quantity exactly.
Oil metering. A turbine flow meter was used to meter oil. Small magnets located on the outer edge of the rotor transmitted signals to sensors in the rotor housing. The latter could then measure the speed at which the rotor turned, and thereby arrive at the exact amount of liquid flowing through the meter.
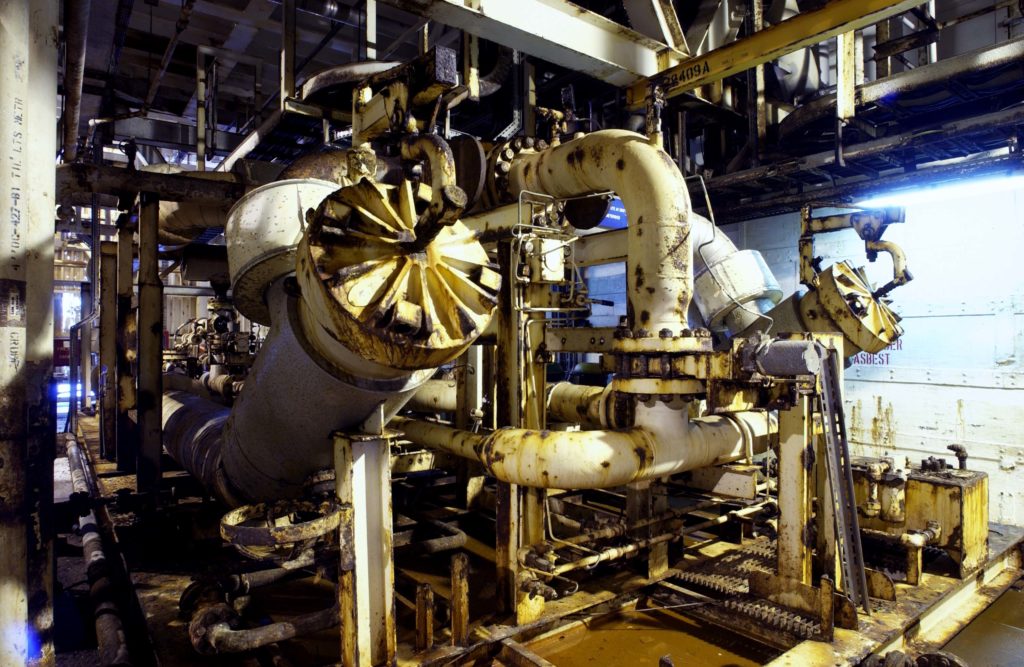
Calibration. Such turbine flow meters had to be calibrated regularly to ensure accurate measurements. Known as a meter prover, this system comprised a horseshoe-shaped test loop which contained a rubber ball.
During calibration, oil was conducted through the loop and pushed the ball ahead of it. Measuring how long the ball took to complete the circuit, given that the loop’s exact volume was known, made it possible to measure oil flow accurately. These data were then compared with the pulses from the turbine flow meter.
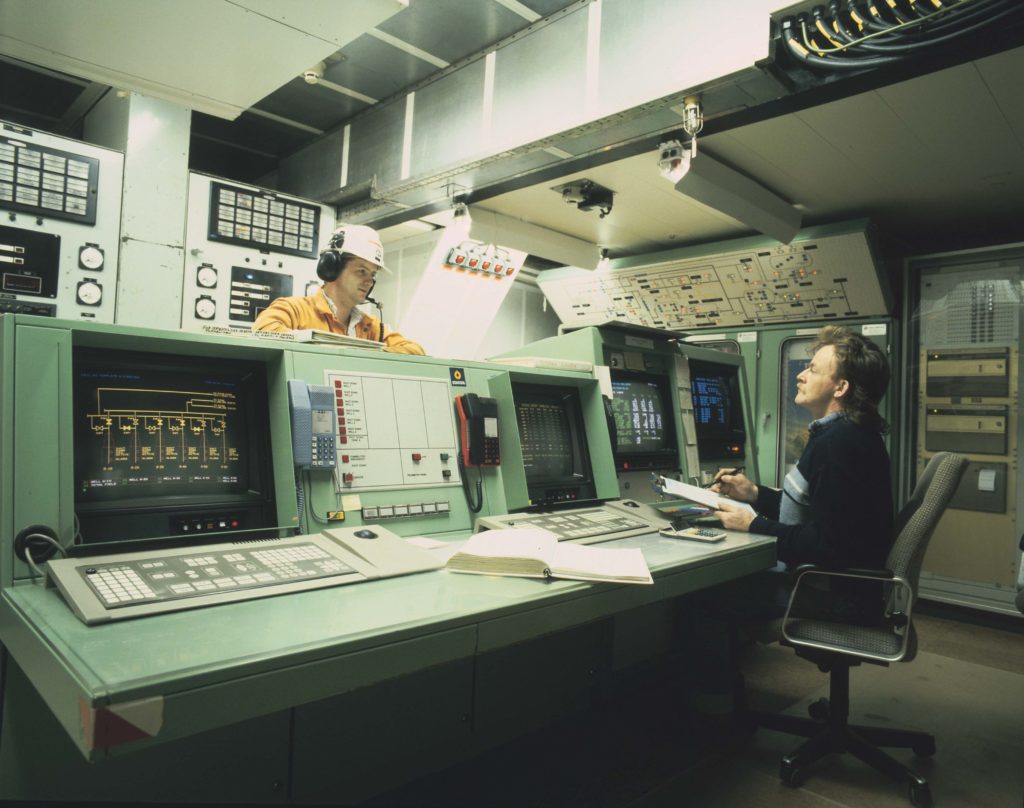
Control room
The control room was the platform’s heart, monitoring and controlling all important processes on board.
Utilities
Glycol regeneration: Glycol coming from the gas dehydration facility had a pressure of 1 205psig and was saturated with water and gas. After its pressure had been reduced, the gas was removed in a degassing pot.
The glycol was then filtered and heated in the regenerator to evaporate the water, and passed through pumps to reach the same pressure as the dehydration unit before being returned to it.
Power supply: Electricity for the platform came from the generator room, where four generating sets were driven by Kongsberg gas turbines. Two of these turbines were later removed and replaced by a diesel engine. Electric switchboards were installed in the module above the generators. The working voltage was 480V.


Pigging:
Gas pipeline pigging. To remove slag and water from the gas pipeline, a sphere was launched into it at 2/7 C and followed the gas flow to Ekofisk 2/4 R where removal took place.
Oil pipeline pigging. The pig in the oil pipeline had a different shape to the unit used for the gas pipeline, but otherwise functioned in the same way.


Other utilities: Other utilities on the platform included fire extinguishing and rescue systems, instrument air, chemical injection and drinking water.
Also provided were diesel and lube oils, gas lift equipment, a workshop, helideck, accommodation module, flare boom, radio communications and so forth.
Tommeliten module
This condensate field lies 11.8 kilometres west of Edda in the Greater Ekofisk area, and comprises the Gamma and Alpha deposits. The first of these was developed with a subsea production system tied back by pipeline to Edda 2/7 C.
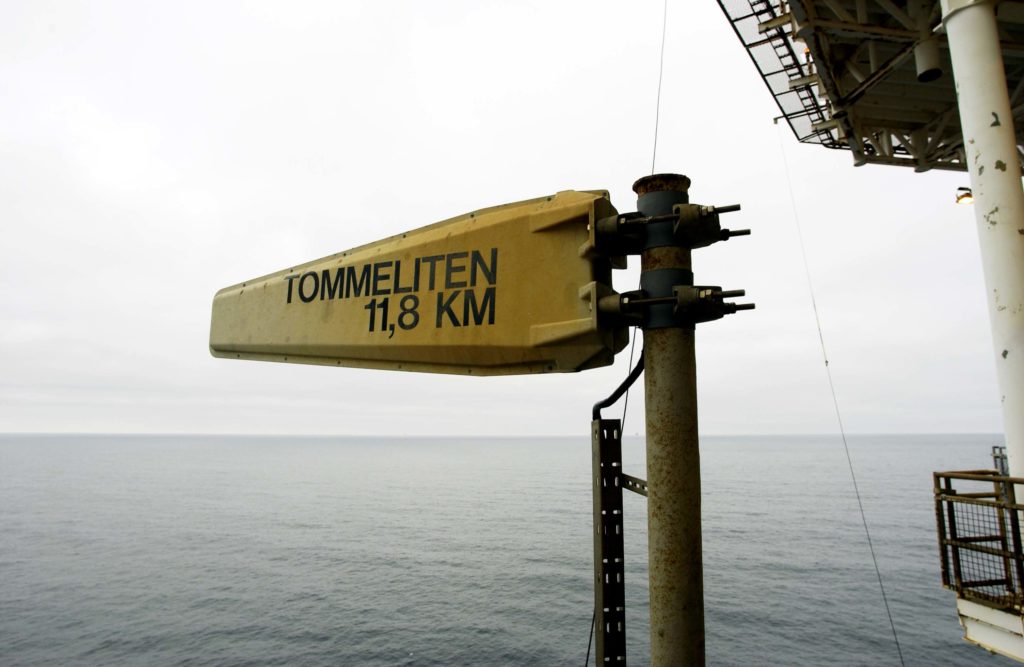
The Tommeliten licensees were Statoil (operator) with 70.64 per cent, Fina with 20.23 per cent and Norsk Agip with 9.13 per cent. Production licence 044 was awarded in 1976, while the development came on stream in 1988.
When production ceased in 1998, Tommeliten had produced 24.4 million barrels (3.9 million standard cubic metres) of oil, 9.7 billion scm of gas and 0.6 million tonnes of natural gas liquids (NGL).
Processing equipment to separate condensate, gas and water from Tommeliten was installed on 2/7 C because the field was too small to justify its own platform. Located only a few kilometres away, 2/7 C also had spare space and capacity. Wells on Tommeliten were operated from a dedicated control room on 2/7 C.
Tommeliten’s process facility was similar to the existing plant on 2/7 C, but smaller. Output from both Tommeliten and Edda was carried in the same pipelines – one each for oil and gas – from 2/7 C to Ekofisk 2/4 R.





