Drilling

The first wells drilled on Ekofisk were relatively primitive compared with today’s examples. They were good in terms of the available knowledge and equipment, but not up to “vacuuming” the reservoir. Drilling horizontally was not possible, for example. Once the well had reached an angle of 70 degrees from the vertical, it was earlier considered almost horizontal. Today, wells are drilled not only with horizontal sections but even angled upwards. The technological trend which made this possible began in the 1980s.
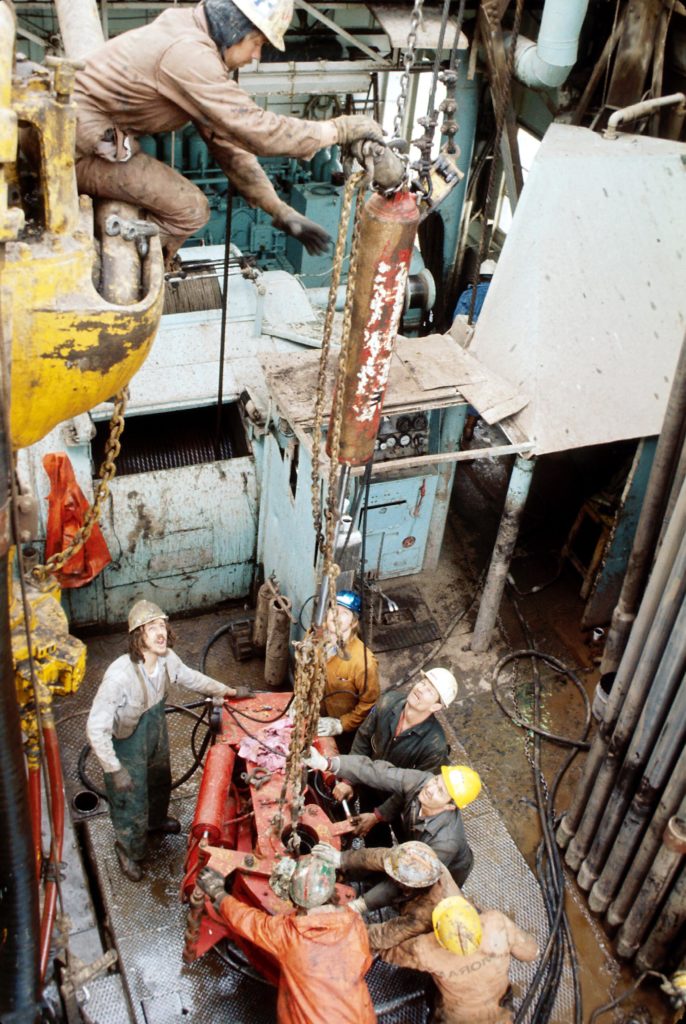
Drilling work on Ekofisk has been conducted by a number of different contractors over the years. Their personnel were responsible for operating the actual rig. The companies used to begin with remained, but changed their names. A case in point was Moran Brothers, which became Morco, Norcem Drilling, Aker Drilling and finally Transocean Drilling during its time on the field.
In 2001, drilling contractors Deutag Norge Drilling, Smedvig Offshore and Mærsk Drilling – now Mærsk Contractors – were involved in the Greater Ekofisk Area (GEA). They had some 500 people working for Phillips in the GEA or on land.
Modern computer technology and fibreoptic cables today allow the operator company to follow offshore activities from its offices in real time.
Dowell, Halliburton og BJ Services have been used for cementing services, while Eastman, Sperry Sun or Target Drilling (part of Aker Drilling) provided directional drilling. Pathfinder was engaged in the latter activity in 2001.
Other drilling-related contractors have included Schlumberger or Atlas for logging and Weatherford for casing services, while Milchem, Ceca, MI and Anchor Drilling Fluids have been among those involved with drilling fluids.
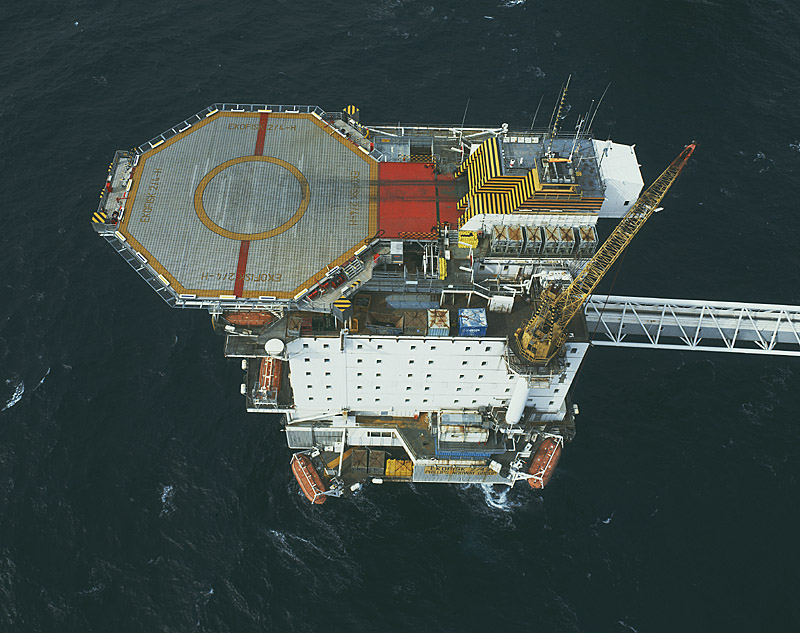
Drilling operations manager
A distinctive feature of the Phillips organisation in the 1970s and 1980s was the presence of a central drilling operations manager for all the installations. Employed by the company, they served on Ekofisk 2/4 H in a coordinating role. They collated reports from all the drilling supervisors and passed them on to the drilling department ashore.
Drilling supervisor
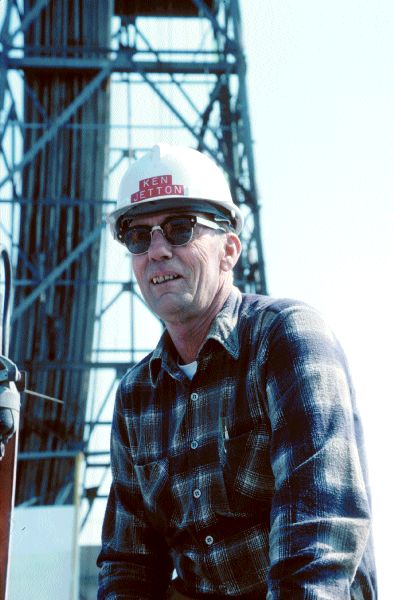
The drilling team was led by the Phillips supervisor. During the early years on Ekofisk, the company only had a single person in this role on board who was on call around the clock. This meant they had a bed in their office and lived and worked there. Following the Bravo blowout in 1977, however, a junior drilling supervisor was introduced who worked the night shift – and was usually called the “night man”. Members of the drilling team were drawn from several contractors specialising in various services. They included the toolpusher, drillers, derrickmen, roughnecks and roustabouts, with support from electricians, mechanics, materials providers and – initially – crane operators.
Toolpusher
The toolpusher is the head of the drilling team, where everyone is employed by the contractor which has been hired for the specific platform. This person supervises the crew and ensures compliance with routines – particularly matters related to safety. Drilling must be conducted as specified in the plans drawn up by the operator in Tananger and approved by the Norwegian Petroleum Directorate.
In close consultation with the drilling supervisor, the toolpusher monitors, collects and registers technical drilling data and stays in constant touch with the operator’s drilling operations manager on Ekofisk. Engineers are called from land for special operations.[REMOVE]Fotnote: Kvendseth, Stig S, Giant Discovery. A History of Ekofisk Through the First 20 Years, 1988. The toolpusher can also relieve the driller during lunch breaks and participates to a varying extent in the work being done.
Driller (drilling and maintenance operator)
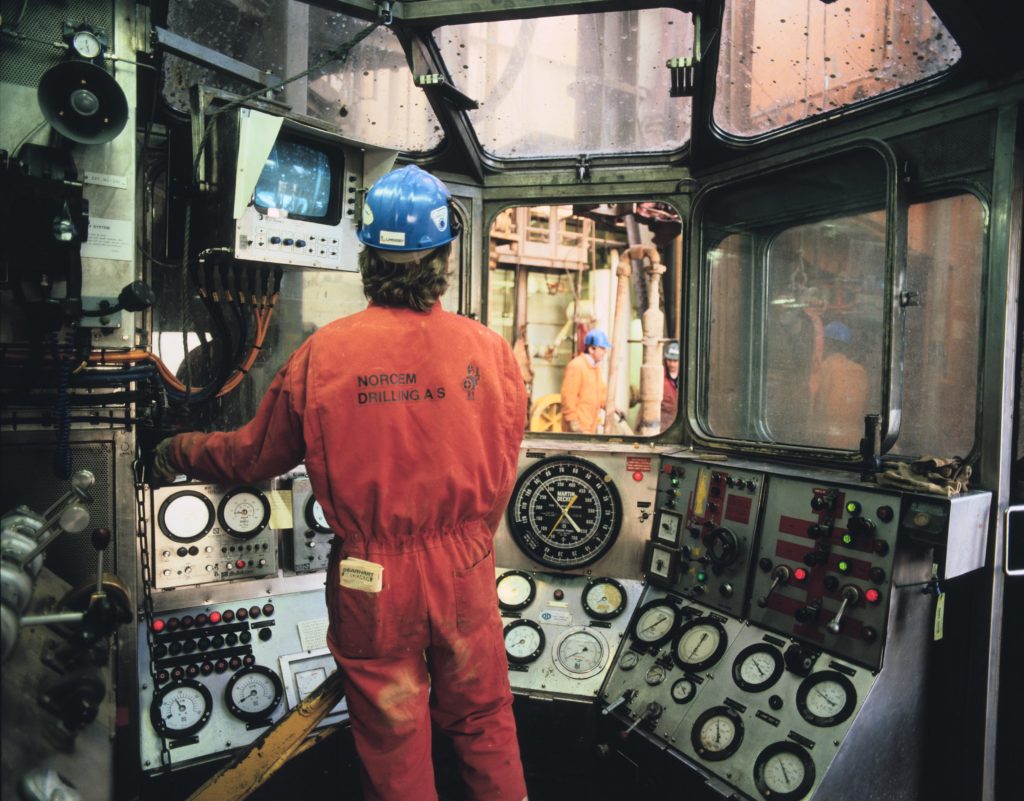
The driller is responsible for day-to-day work in accordance with the toolpusher’s instructions. From the driller’s cabin, they operate the equipment used to drill wells. That includes maintaining control of the various drilling parameters, such as pressure, drillability, torque and mud flow, and ensuring that everything functions as it should. When Norwegian drilling contractors entered this business, they extended the drilling team with the addition of an assistant driller function.
One trend from early exploration drilling off Norway down to the present time has been that less and less of overall rig time is devoted to running the drill string in and out the well. Not only is the bit not replaced as often as before, but it has also become possible to carry out downhole measurements during drilling. Although the whole string must still be pulled to replace the bit, the latter is now more durable thanks to improved knowledge of how it wears and the improved quality of this product.
Today, much of the work is conducted from a modern driller’s cabin with chairs designed on physiological principles to be occupied for 12 hours. The drilling equipment has become computer-operated with the aid of the joystick and keypads on the arm rests.
Much of the work previously done on the drill floor by the roughnecks, roustabouts and derrickmen has been automated through the use of robots.
Drilling represents the main activity up to the stages of completion for production, test output, pressure support and/or well plugging. A qualified drilling and maintenance operator should be able to participate in all phases of drilling, including managing and maintaining drilling mud and mud systems and doing first-line maintenance on pressure control systems and equipment.
Directional drilling and MWD
Directional drilling of production wells makes it possible to drain more extensive areas of an oil or gas reservoir from a single installation. This technology for diverting the well from a vertical path began to be developed in the late 1980s. Specialists in utilising it are usually operator company employees.
The method starts out like normal rotary drilling, but then transitions to a phase where a specified angle from the vertical is built up. During this stage, the drill string is not rotated. The bit is turned instead by a turbine installed immediately behind it, with the vanes driven by the mud pumped down the string. Rotary drilling resumes once the desired angle is reached.
Horizontal drilling is a further development of the directional approach which makes it possible to reach all parts of a reservoir. This method is important in some formations where the oil may be located in thin layers, and allows the recovery factor for the field to be substantially increased.
Baker Hughes Inteq has developed a solution called AutoTrack, where the bit is guided by a steerable system which allows direction and angle to be adjusted continuously while drilling. Sensors on the drill string analyse the rocks being drilled, and computerised commands then steer the bit into the correct geological structures.
A measurement while drilling (MWD) engineer uses the equipment required, and processes, presents, evaluates and quality-assures the data acquired and sent back to the surface. Directional measurements provide information on the direction (azimuth) and angle (inclination) of the well to help the driller steer the well along its planned path.
A number of different sensors measure various aspects of the formation being drilled. Presented as curves in the logs, these data are used in formation evaluation. This means they are interpreted to determine the type of rocks involved (such as sandstone, claystone or carbonates), what they contain (water, oil or gas) and other properties such as permeability.
The logs are interpreted both by the MWD engineer and by geologists offshore, as well as petrophysicists and geological specialists on land. Along with analyses of the drill cuttings – rock chips removed from the well – collected by the mud logger, these data provide a good picture of the formation surrounding the well.
MWD information is often used actively by geologists to keep the well concerned in the desired formation layer. This is known as “geosteering”. Measurements transmitted to the surface can be utilised to optimise well parameters and reduce damage to the downhole equipment. Pressure readings could also indicate if the well is being cleaned properly – whether cuttings are being transported out or are accumulating downhole and may cause equipment to get struck.
Introducing AutoTrack from the mid-1990s allowed the string to be rotated and steered simultaneously and opened completely new opportunities in directional drilling and geosteering. This is an example of the rapid advances made with MWD equipment in recent decades. New technology and applications for the information acquired are continuously being developed.
Derrickman
This person had two main jobs – participating in tripping (pulling out the drill string and running it back in) and ensuring that the drilling mud was correctly blended. During tripping, the derrickman worked in the derrick with the driller and roughnecks on the drill floor. The string was pulled out of the well and broken down into stands – lengths of three drill pipes screwed together. The derrickman’s job was to receive these stands and secure them in a “fingerboard” high up inside the derrick, and then to release them when the string was to be made up again.
This was fairly heavy work, conducted from a small platform measuring a square metre located 30 metres above the drill floor. He had to lean over the edge, with a rope to prevent him falling. Mechanisation and automation of drill-floor work began in the mid-1970s. That include mechanising the derrickman’s duties during tripping. He now controls a mechanical pipehandling system which grips each stand and positions it in the fingerboard as the string is pulled out – and vice versa.
When the derrickman is not involved in tripping, he works in the mud room to ensure that drilling fluid is always blended in accordance with the drilling engineer’s instructions.
Roughneck
The roughnecks did the heavy manual labour on the drill floor and the cellar deck below. When making up and breaking out drill pipe, they attached the tongs used for this work by the driller.
At the beginning of the 1970s, the roughnecks went over to using a “spinner”, a hydraulic device used to screw together and unscrew lengths of drill pipe.
Two-three roughnecks worked on setting the slips – a moveable wedge-shaped locking device which weighs between 40-50 kilograms. This holds the drill string in the rotary table when it is not suspended from the
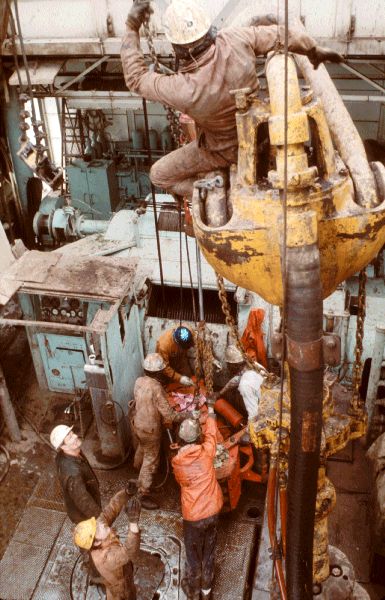
derrick’s travelling block (crane).
The roughnecks were also responsible for cleaning and maintenance on the drill floor (which was washed with caustic soda and diesel oil). In addition, they could be drawn in to help the service companies in their various activities. Various equipment units were installed and readied by the roughnecks on the cellar deck under the supervision of their superiors or specialists. This work included installing various sizes of blowout preventers (BOPs). The cellar deck was also where risers were attached.
Various dimensions of casing were hung off, Xmas trees (valve assemblies) installed and high-pressure hoses attached to conduct hydrocarbons to the outside of the rig during testing. Otherwise, the roughnecks helped to blend drilling mud and to keep an eye on the shale shaker – a vibrating screen which cleans mud returning from the well.[REMOVE]Fotnote: Kvendseth, Stig S, Giant Discovery. A History of Ekofisk Through the First 20 Years, 1988.
A lot of this work is now being handled by an “iron roughneck” – a robot controlled by the driller from their cabin. But the human roughnecks must still move about the drill floor – partly to lubricate various items of equipment.
Cementers/well operators
Cementing forms part of the whole process from exploration drilling, via completion for production, to subsequent downhole maintenance work. Well operators involved with cementing are the last people to leave a platform after the wells have ceased production and been plugged with cement. The cementer’s job is varied and makes big demands on theoretical and practical skills. It can be split into three main areas: cementing, pressure testing and use of downhole tools.
Drilling a well starts with large bits (75-90 centimetres in diameter), which are progressively replaced with smaller ones as the borehole advances. The smallest is usually 15 centimetres.
When changing to a smaller bit, the whole drill string is pulled out and the borehole is lined with steel tubes called casing. A casing string can be several hundred metres long.
Before drilling resumes, cement is pumped into the annulus (gap) between the well wall and the casing in order to anchor the latter solidly in place. The cement prevents the borehole from collapsing, and stops any uncontrolled flow of oil and gas reaching up to the surface outside the casing string.
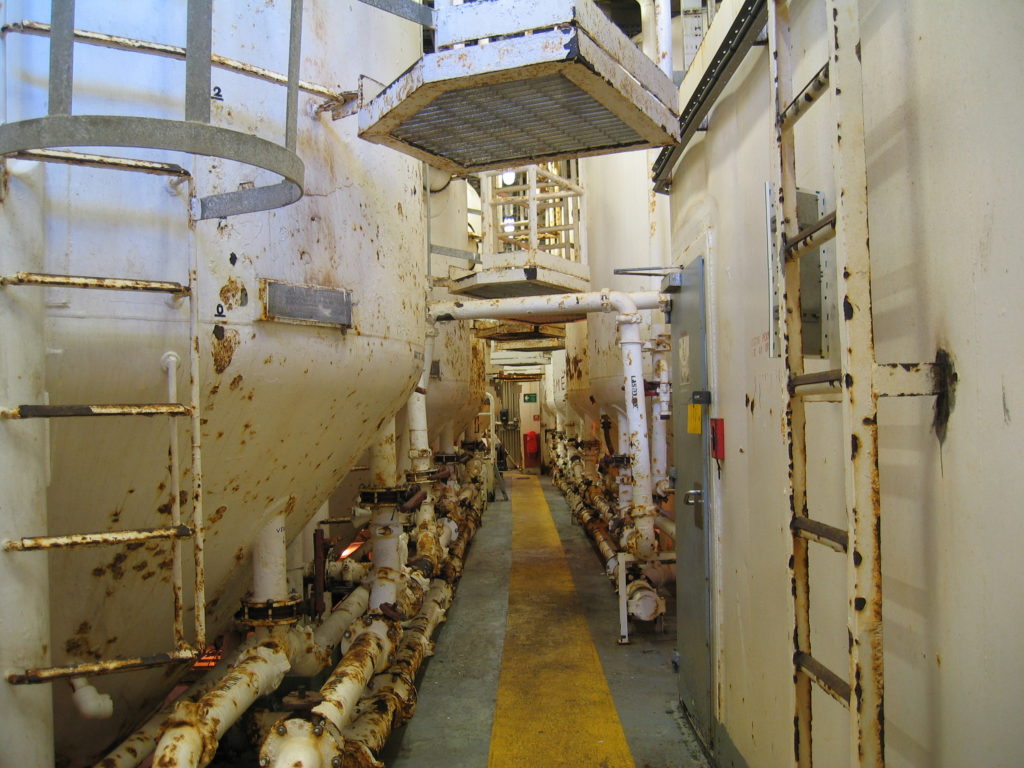
Cementing is normally a straightforward job. The volume to be filled gets calculated in advance, and all that then remains is to pump down that quantity. Since the work has to be done quickly, being well prepared is important. The person leading the cement job previously had to know the pump more or less intimately. This pump has to work efficiently (in terms of the number of pump strokes) the whole time in order to be certain that the whole annular space around the casing is cement-filled. Problems would otherwise arise in the well later.
Today’s cementing pumps are electrically powered and their pumping efficiency can be determined with the aid of instruments. Drilling mud is needed to pump cement. When changing from one tank to another, valves have to be closed and opened. That creates a pressure.
Casing operator
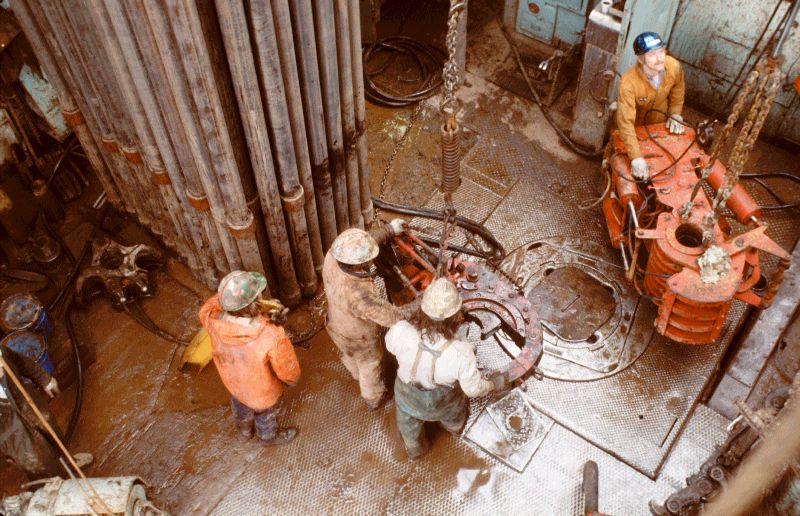
As the well advances, casing is run into it and cemented in place. The diameter of this steel tubing diminishes with increasing borehole depth. Casing is intended to prevent the well from collapsing, and it also provides an important return channel for the mud which has been pumped down inside the drill string. In addition, it isolates problematic zones in the rock formations – such as areas where the pressure is particularly high or low.
Casing is delivered by specialist companies, which calculate how many lengths of each tube type will be required for a well and ensures that the equipment is in place at the right time. The casing operator handles the tubes, but this job has become more automated in recent years.
Mud loggers and geologists
The job of the mud logger or engineer is to acquire well data from instruments located either on the surface or down the borehole in order to determine pressure in the rock’s pores. Parameters monitored include well depth, drilling speed, weight on the bit, rotation speed, mud density, gas content in the mud, and how fast drill cuttings move from bit to rig.
Continuous observation of this information can identify unstable downhole conditions, and possibly prevent accidents such as uncontrolled blowouts or a well collapse which traps the drill string. These parameters can also indicate geological variations. If drilling speed suddenly picks up while drilling through a shale layer, for example, this could mean that the bit has entered sandstone – which is a reservoir rock. Among the mud logger’s jobs are the collection and washing of drill cuttings for analysis by the rig’s geologist in order to obtain an overview of the rocks drilled through.
Well loggers
Logging involves running instruments into the well in order to measure various physical properties of the reservoir strata or their contents (oil, gas or water). Examples of the information sought include natural radioactivity, rock density, the speed of sound, electrical resistivity and temperature.
Logging can be conducted under various conditions:
- logging while drilling (LWD) – using instruments attached to the drill strong
- open-hole logging – after drilling but before the casing and production tubing has been set
- production logging – to measure such parameters as fluid flow from various parts of the reservoir.
Well testing
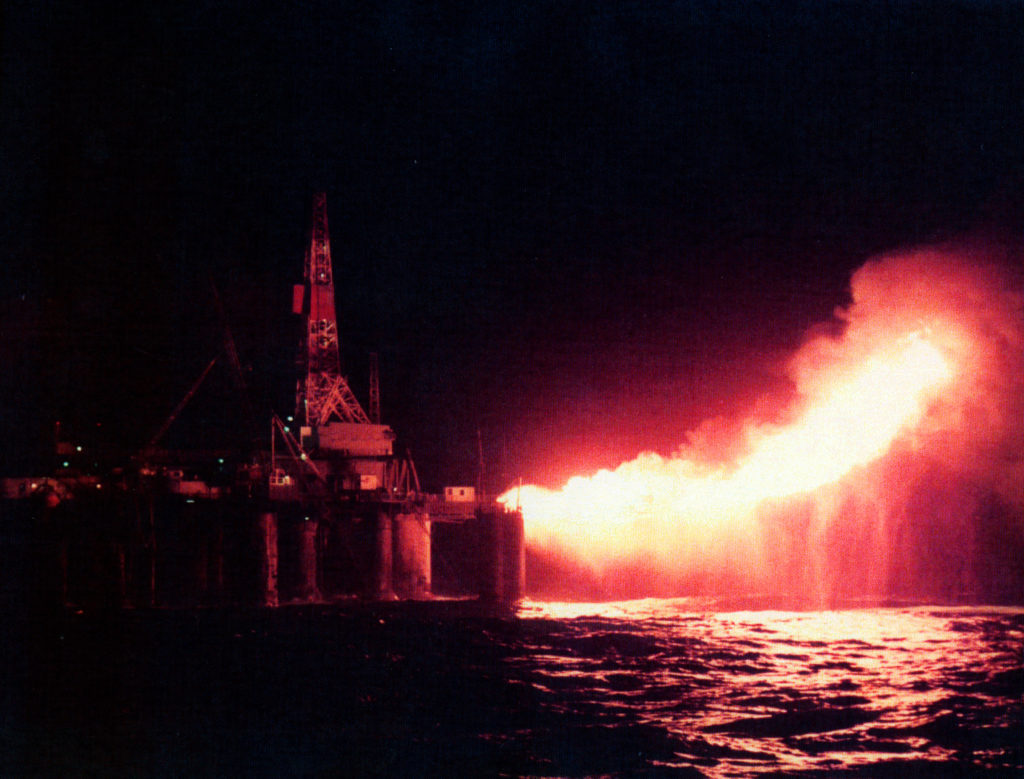
If logging and possible rock cores extracted from the well show that some of the rock strata deep below ground contain oil and gas, the usual practice is to conduct a production test. This is done by allowing the oil and/or gas to flow up to the surface under controlled conditions. Such parameters as how fast the well flows are measured and samples of the oil/gas taken.
The work is usually led by a reservoir engineer, and normally takes place after exploration drilling ends. The well is then plugged with cement, the seabed cleaned up, and the site left.