Seabox – research project for seabed water treatment
However, a large and heavy plant is needed to treat the seawater used for such waterflooding. That requires a lot of space and energy, and is thereby expensive.

Seabox concept
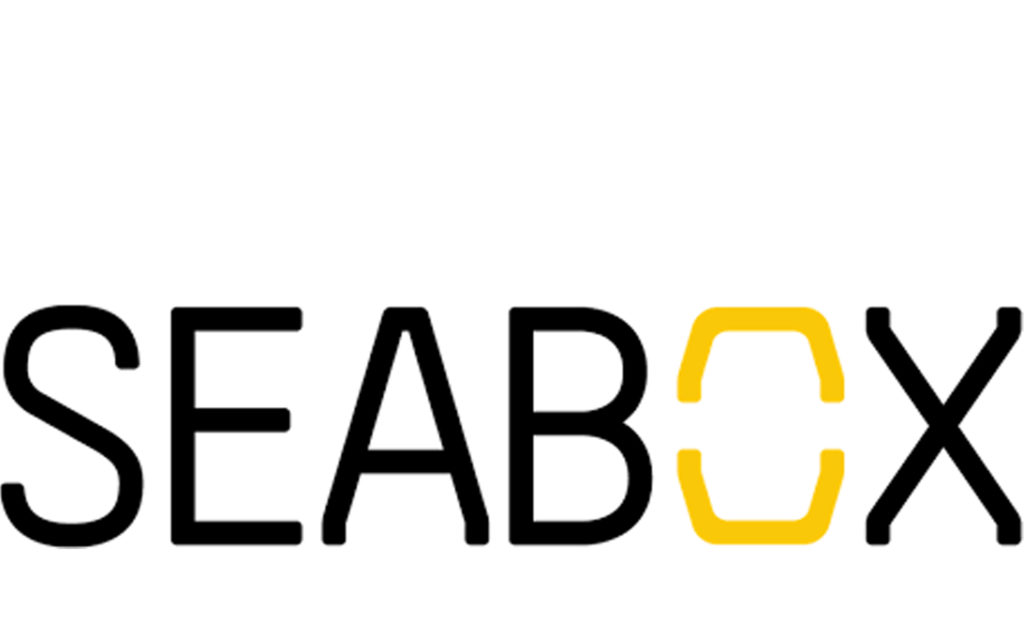
Moving the whole seawater treatment plant to the seabed was the solution which occurred to David Pinchin and Helge Lunde in the early 2000s.
Producing from subsea wells and placing parts of the process on the seabed had become increasingly common. So the question was whether the same could be done for treating seawater.
Performing this function at source and with the injection well close at hand, without having to pass via a platform, was an attractive thought – particularly given the volumes involved.
With that in mind, Pinchin and Lunde established the Seabox company in 2004 to develop a complete subsea treatment, processing and injection module.
This project received backing from the Research Council of Norway and several oil companies. That meant long-term tests of the technology could be conducted by the Norwegian Institute for Water Research (Niva) in the Oslo Fjord in 2010 and 2013.[REMOVE]Fotnote: Teknisk Ukeblad, “Seabox”, 16 May 2016.
National Oilwell Varco acquired a stake in Seabox in 2015, and the company secured further support from Norway’s Demo 2000 research programme as well as several oil companies.
The latter included ConocoPhillips, and the aim was to build a prototype in order to qualify the technology for treating water on the seabed.
Seabox. This subsea treatment plant can produce sulphate-free seawater with the aid of microfiltration and membranes.
Seawater must be treated before injection into a sub-surface formation to prevent undesirable bacterial activity and to avoid particles which could block pores in the reservoir.
If barium and strontium are present, for example, untreated seawater can cause chemical reactions in these “soft” metals with oversaturation of salts and minerals in the reservoir water.
That in turn could block the formation pores should pressure and temperature fall, which poses the risk of reducing or losing production.
A reservoir can also “go sour” if sulphate-reducing bacteria are allowed to flourish. That not only increases production costs but reduces the value of the hydrocarbons produced.
Treatment process
The Seabox process uses electricity to produce chlorine from salt water in electrolytic cells. Seawater being treated spends up to two hours in the presence of this chlorine.
That kills the bacteria before the water is exposed to hydroxyl radicals (OH molecules), which ensure that all organic material is killed and dissolved.
In practice, this removes all bacteria and most of the particles in the first stage of the process. The water then passes through a microfiltration plant and nano- or RO-membranes.
Everything takes place inside the box, which eliminates emissions or discharges. The treated water is virtually fit to drink.
Ekofisk test well
Seabox received one of the most distinguished awards at the Offshore Technology Conference (OTC) in Houston in 2018, as well as a contract with ConocoPhillips.
The latter assignment covered a first unit which would be put into test production on Ekofisk.[REMOVE]Fotnote: Teknisk Ukeblad, “Seabox ble den store vinneren i oljeindustriens ‘Oscar’”, 30 April 2018. At that point, almost NOK 300 million had been devoted to developing the concept.
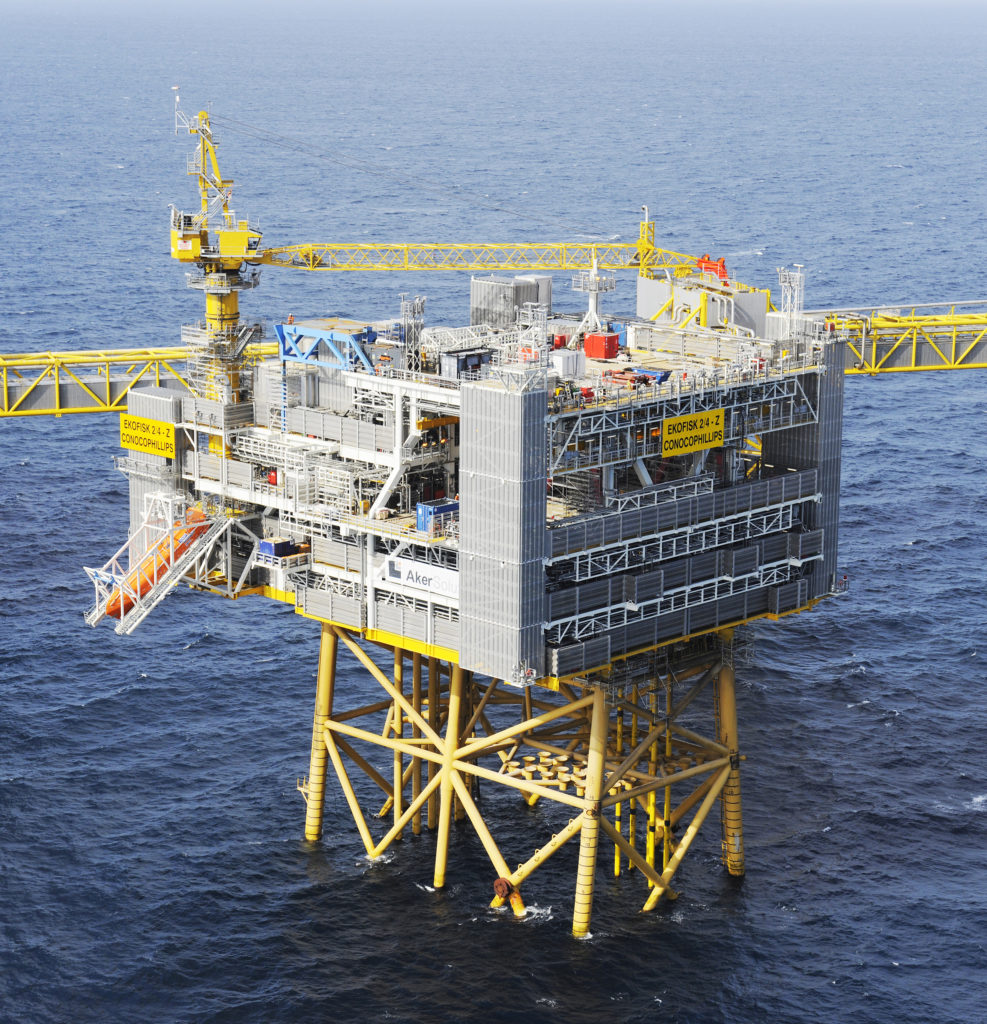
ConocoPhillips made a platform and a well available for the research project, and the Seabox unit was installed on the seabed in August 2018 close to Ekofisk 2/4 Z and the West Linus rig.
In the first instance, treated seawater was conducted up to the rig to have its quality checked. Once it had passed muster, treated seawater began to injected in well Z-02.
This was a former production well which had been converted for injection. The project continued until August 2019, and its results will be significant for future work.[REMOVE]Fotnote: Pionér, no 3, 2018.
Field operator of the yearEkofisk South – 2/4 VC starts up