Ekofisk field organisation, 1973-98

Some key steps along the way will be addressed below, starting with the establishment of the Ekofisk Complex in 1979 at a time when developing the whole area was in full swing.
In 1986, development of the Greater Ekofisk Area (GEA) was approaching its peak for both the number of facilities and the size of the offshore workforce.
The final date is 1994, when the GEA had reached a mature phase characterised by downsizing and periodic restructuring in order to achieve optimum operational efficiency.
Organisational change has naturally continued since then. But the last step in this context came in 1998, when the first phase of the GEA’s history based on “old-fashioned” technology ended.
That was when Ekofisk II came on stream, with the company adopting all the opportunities offered by modern computer technology.
Bringing new platforms on stream and shutting down old facilities have naturally influenced the current composition of the company’s offshore organisation. But that falls outside the scope of this account.
First production phase – 1973
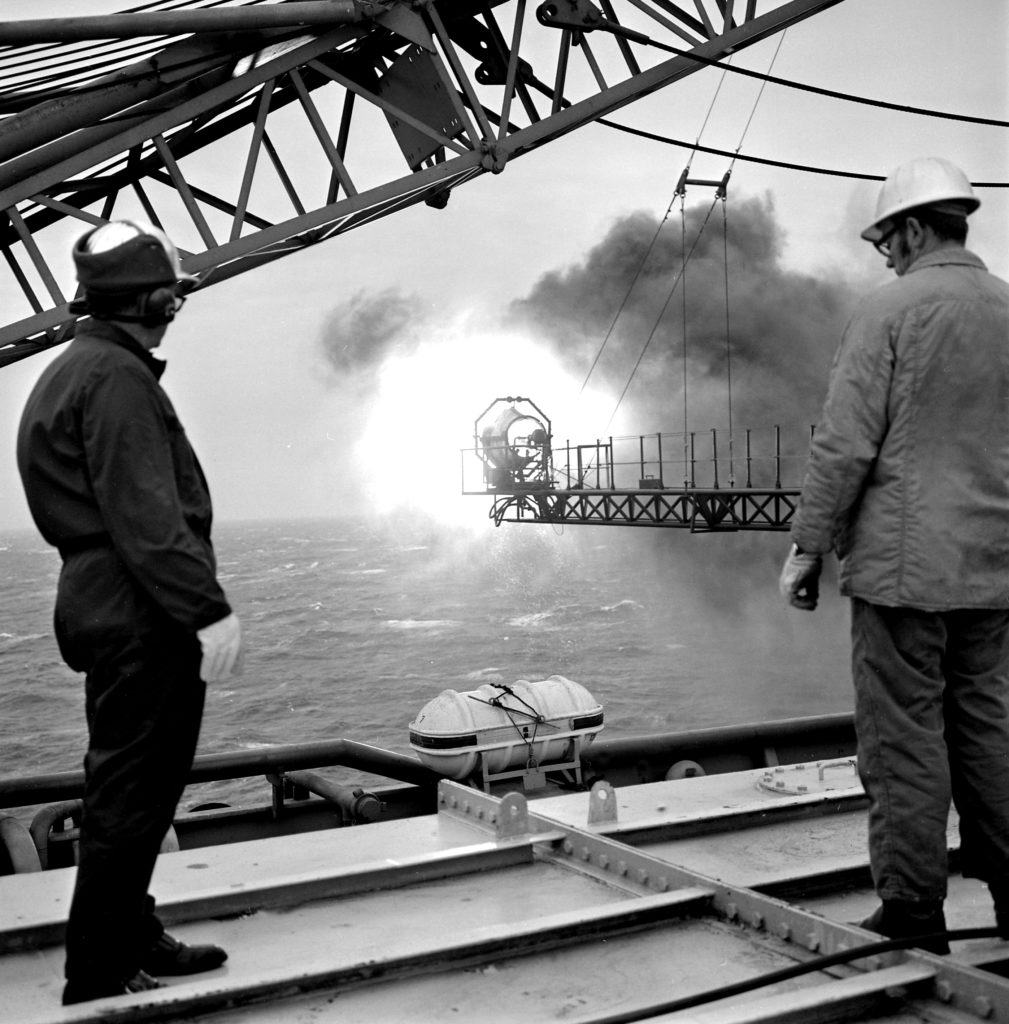
Trial production from Ekofisk via Gulftide began on 14 June 1971, and regular operation started from well A-13 on Ekofisk 2/4 A in April 1974.
When initial output commenced, a relatively large number of people were recruited to the Phillips field organisation – including 12 Norwegians.
These new employees received training both on land and offshore, while equipment was tested before operations began on the various installations.
The first organisational chart for Phillips personnel dates from 1973, when Ekofisk was in its early production phase. Gulftide stayed on stream until the fixed platforms took over.
Construction of Ekofisk 2/4 A (Alpha), 2/4 B (Bravo), 2/4 C (Charlie) and FTP (Field Terminal Platform) began in 1972, along with the northern and southern flare stacks. They became operational in 1974.



The Ekofisk 2/4 Q (Quarters) platform became operational during the hectic development phase in 1973 along with the Ekofisk tank, which provided oil storage in 1974-77 before being converted for processing.
Finally came West Ekofisk 2/4 D, which was installed in 1973 and came on stream in 1977.
During this period, characterised by the need to get going, the field organisation was headed from land by the manager Ekofisk operations.
No central leadership existed offshore, with the heads of the drilling and production, maintenance, and safety functions reporting directly to the shore-based management.
Drilling and production was divided into three separate units which had little do with each other in practice. Phillips personnel were in charge of drilling, but the bulk of the work was done by contractors.
Most production workers were Phillips employees, while the third unit dealt with marine operations like offshore loading and diving.
Also largely handled by operator personnel, maintenance was split into a number of sub-departments such as electrics, metering, and instrumentation and communication.
In addition came maintenance planning, offshore stores and, naturally, such skilled trades as welders, mechanics, crane operators, electricians and instrumentation technicians.
The safety department comprised a handful of people who inspected tools and equipment and monitored safety routines.
Expanding and strengthening (1979)
Most of the GEA installations were in place by 1979. Production was in full flow, with direct pipelines to Teesside and Emden for oil and gas respectively.
Three booster platforms – Ekofisk 2/4 P (Papa) at the Ekofisk Complex, Norpipe 36/22 A and Norpipe 37/4 A – were installed on the Teesside line in 1974 and became operational the next year.
In the same way, the gas pipeline to Emden, which opened in 1977, was provided with the B11 and H7 compressor platforms at points along its length.
New facilities installed in 1975 and brought into operation in 1997 were Cod 7/11 A, Ekofisk 2/4 R (Riser), Tor 2/4 E and Eldfisk 2/7 A.
Eldfisk 2/7 B, Albuskjell 1/6 A and Edda 2/7 C followed in 1979, while Ekofisk 2/4 H (Hotel), Albuskjell 2/4 and Eldfisk 2/7 FTP were positioned in 1977.
The hotel, with cabins, offices, cafeteria and so forth, was operational in 1978, and the other installations followed the next year.
Offshore activities expanded enormously during these years, and the organisation grew correspondingly. New structures became necessary to keep the whole business manageable.
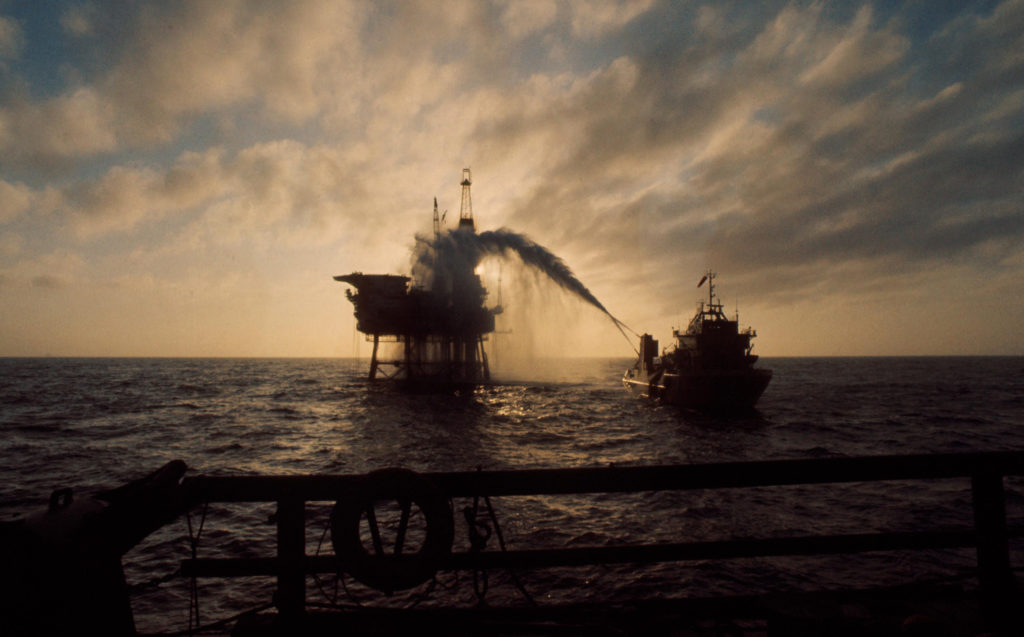
The Bravo blowout – the first uncontrolled release of oil and gas on the NCS – in 1977 led to a safety-driven strengthening of personnel for drilling and maintenance.
Contractors also increased their workforces. But the operator employees responsible for day-to-day operation were already well staffed and did not need reinforcing to the same extent.
Extensive and growing activity meant the field organisation gained its own operations manager offshore (OMO) – a post shared between three people because of the tour rotation.
The OMO reported in turn to the drilling and production manager on land, and was responsible for no less than 10 departments.
They covered production Ekofisk Complex, production north and south, drilling, marine operations, safety, planning, pipelines, maintenance, administration and engineering offshore.
The first of these units, covering the central complex, had superintendents on both day and night shift who were in charge of production supervisors and operators.
Covering the outlying platforms, the production north and south department comprised the same types of personnel as well as wireline specialists, who usually reported to drilling.
The latter department had risen from nine drilling supervisors in 1973 to 36 by 1979, which cannot be explained by the increase in the number of installations.
After the Bravo blowout, the arrangement with such personnel being on call around the clock was replaced with day- and night-shift drilling supervisors to improve safety.
Marine operations personnel largely dealt with diving. Once the Teesside pipeline had been installed, offshore loading of oil into tankers ceased.
The safety department was reinforced after the Ekofisk 2/4 A fire in 1975 and the Bravo incident two years later. In addition to the supervisor, it had 26 safety representatives in 1979 compared with only two plus two inspectors in 1973.
Coordination of all work orders was handled by the planning department. That included determining what materials should be used and ensuring their availability.
This department also planned staffing of jobs, budgeted how many hours each assignment should require, and subsequently kept records of the time taken.
The pipeline department controlled the oil and gas systems to Teesside and Emden respectively, and was staffed with inspectors and operators.
Maintenance was a big department, with personnel spanning many categories – including technicians, crane operators and electricians.
Among other disciplines were instrumentation technicians, machinists, mechanics, painters, roustabouts, telecommunication technicians and welders.
The administration department was largely run from 2/4 H, where staff dealing with personnel movements, freight logistics and sea/air traffic were located.
Vessel coordinators, logistics managers and radio operators were based in the control room above the helideck, while receptionists sat in the Sky Lobby.
However, safety representatives and the medic (nurse) were spread between the various field installations.
The offshore engineering department did technical planning. A good deal of that took place on the spot at this time of high installation activity, but is all generally done on land today.
Staffing of the department comprised electrical, process, production and reservoir engineers, laboratory and calibration personnel, and inspectors for equipment safety.
Organisation in the mature phase (1987)
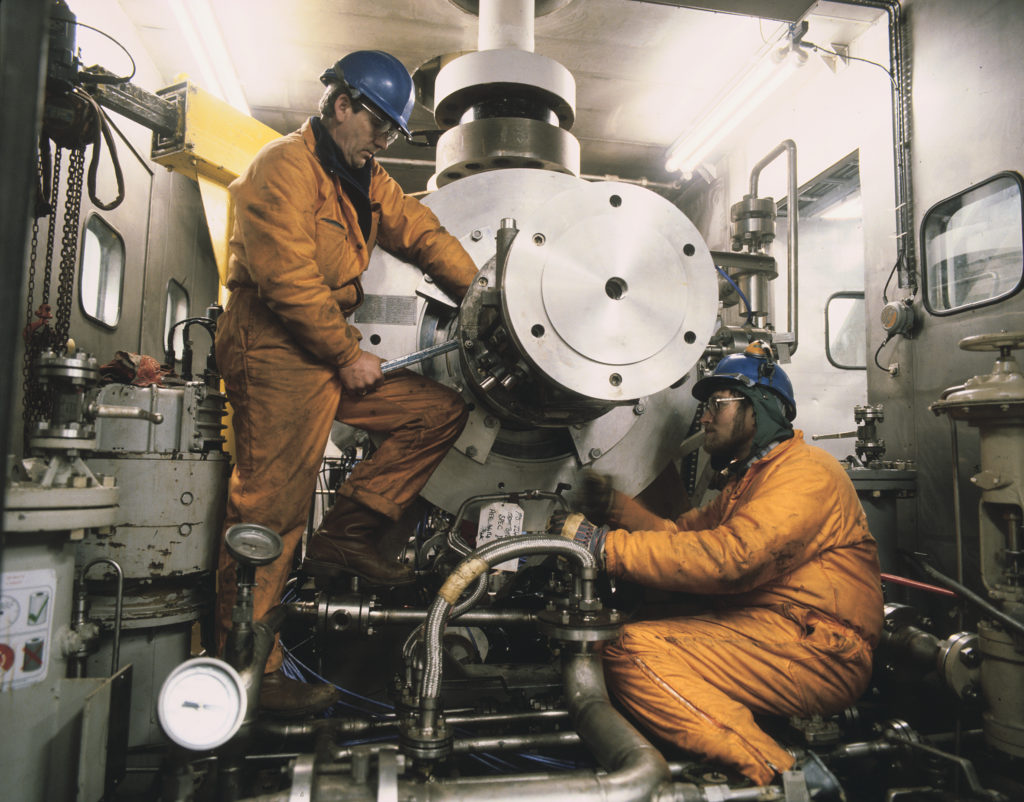
By 1987, Ekofisk has moved into a mature phase, with growth no longer as hectic as before. The Ekofisk 2/4 G and 2/4 S platforms, operational in 1981 and 1985 respectively, were more to be regarded as adjustments.
However, new challenges arose. A key question was how the highest possible recovery factor for the field should be achieved. Waterflooding was tested on Ekofisk 2/4 B before full adoption.
Ekofisk 2/4 K (Kilo), with a drilling rig, water injection and accommodation module, was installed in 1986 and became operational in 1987.
At the same time, it was discovered that the whole seabed over Ekofisk was subsiding. An operation to jack up the platforms was planned in 1986 and implemented the following year.
In 1987, the field and GEA management was based at the Ekofisk Complex, with an offshore field manager (OFM) in overall charge of departments for administration, engineering, production, utilities, safety, drilling and head safety delegate (HVO).
The production or operations department was the biggest, with the operations units for the Ekofisk Complex and the other platforms reporting to it.
Each operations manager post was held by three people. An individual manager would be offshore for 14 days, have three weeks off and spend a week at the office on land in each rotation.
This meant that the onshore and offshore organisations kept in better touch with each other. They were also reinforced by an operations coordinator to handle personnel matters.
Another major change was appointing an offshore installation manager (OIM) for each platform from 1983. Reporting by the various disciplines now went through the relevant OIM rather than independently to the field management.
While the platform manager had previously had overall responsibility in the event of an accident, each discipline team had reported to its own superintendents.
There were 12 organisational units in 1987 with their own OIM – Complex South, Complex North with H7 and B11, Eldfisk 2/7 A plus FTP, Eldfisk 2/7 B, Edda 2/7 C, Ekofisk 2/4 A, Ekofisk 2/4 B plus K, Tor 2/4 E, Albuskjell 2/4 F, Albuskjell 1/6 A, West Ekofisk 2/4 D and Cod 7/11 A.
That created more orderly reporting lines. But extensive communication was still needed between the various discipline teams in the GEA and their counterparts on land.
While the formal reporting routines went through the field management, an effective organisation also called for direct links outside these “official” channels.
Generally speaking, in fact, communication was and remains very important in an organisation where several people cover each post.
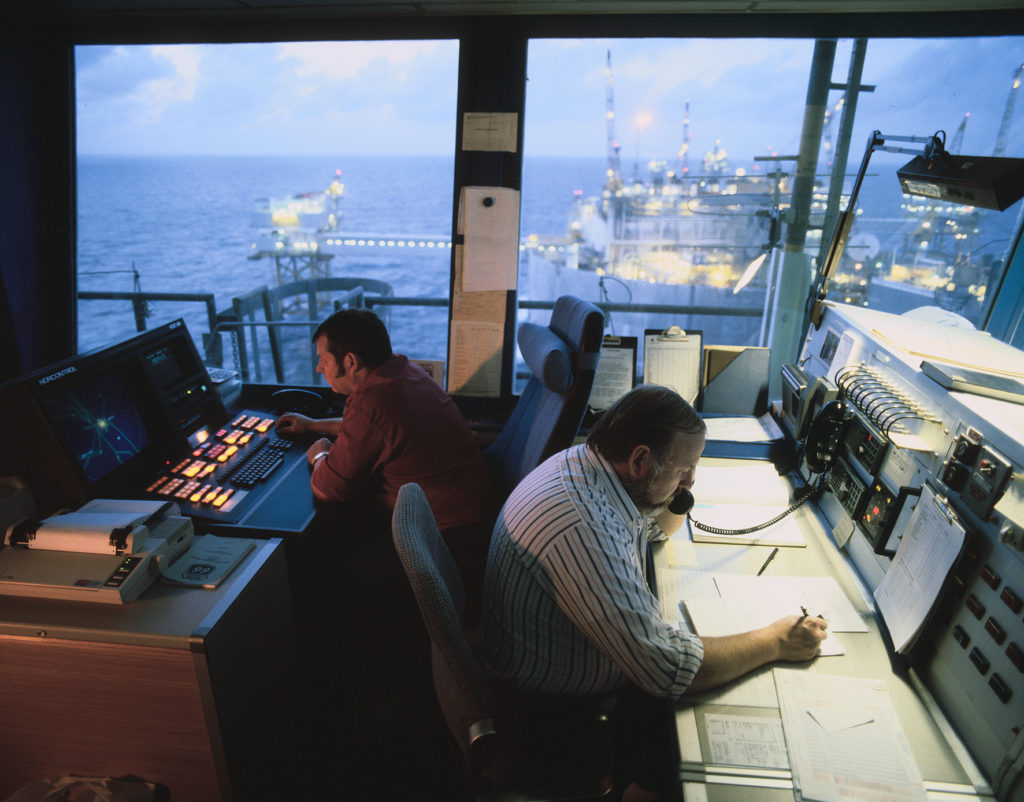
Administration department. This had more or less the same functions as in 1979, with management, receptionist, radio operator, safety officers and medical personnel.
One change was the division of vessel coordination into air traffic and offshore transport. New functions included an operator of the manpower tracking system (MTS) and union representative.
Head safety delegate. A full-time post as HVO was initially introduced by the Ekofisk Committee, the union which organised most Phillips employees, and reported directly to the OFM.
Safety department. The Alexander L Kielland disaster in 1980 boosted the attention paid to safety at every level. But more emphasis was given to shaping people’s attitudes through training and to introducing internal control systems than to increasing the number of inspectors.
While the safety department offshore appeared to have been weakened from 10 people in 1979 to six-seven, the corresponding unit on land had become much larger.
Drilling and wireline. A complex hierarchical structure prevailed here. All drilling supervisors reported to the drilling operations manager at the Ekofisk Complex, who answered in turn to the OMO. The onshore department carried great weight on technical issues.
Technical support. The investigation of an accident where scaffolding collapsed revealed that the division of responsibilities at the Ekofisk Complex had become diffuse.
That led to a reorganisation of the maintenance department. Such work had always lain under the OIM on the outlying platforms, and a similar system was adopted for the whole organisation.
General maintenance at the Ekofisk Complex was assigned to the operations department, which took responsibility for roustabouts, mechanics, and general electrical and instrumentation work.
The remaining maintenance functions were renamed technical support, with seven sub-sections: planning and design, computerised and electronic control systems, machine shop and cranes, communication, stores, turbines and the electrical system.
Some structural changes were also made to the engineering department. It incorporated marine operations as well as painting, instrumentation and calibration, lab personnel, product, process and process control unit (PCU) engineers, and technicians as well as the inspection section.
Downsizing the organisation (1994)
The offshore organisation was being downsized throughout the 1990s. Ekofisk was no longer under development, with work to remove the threat posed by seabed subsidence completed when the breakwater around the tank was put in place in 1989.
In addition, the Ekofisk Complex acquired its own water injection platform when one of the bridge supports to the southern flare stack was given a new topside in 1989 and became operational as Ekofisk 2/4 W in 1991.
The Norwegian Petroleum Directorate (NPD) ordered Phillips to cease operations on the Ekofisk tank within a specified time. That meant new solutions had to be found.
Issues raised included what new investment would be needed, and how long Phillips and its partners could expect to retain their licence for the area.
Since oil prices were also moderate, a number of critical questions were asked about the field’s profitability and even greater attention than before was paid to rational operation.
At the same time, the feasibility of trimming the organisation was enhanced by technical advances with information technology, including satellite transmission and computerisation.
Personnel on land and offshore could therefore increasingly communicate and be on line with each other. Phillips committed big sums to developing a functional internal computer network.
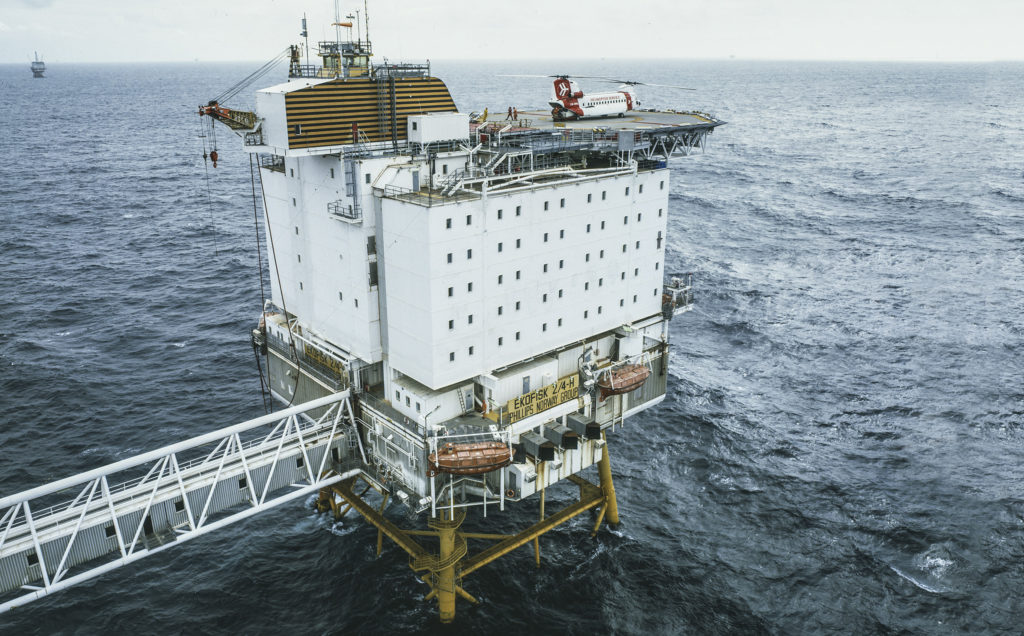
One consequences of these communication developments was that the post of OMO, with its office on Ekofisk 2/4 H, was abolished in 1994.
This person had travelled around the various platforms and was contacted in the event of an accident. But better communication links meant their work could just as easily be done from land.
The only difference was that travel out to the field in the event of an accident added an hour to the time taken to reach the scene.
Simplifying the organisational structure in this way removed a link in the reporting chain, and also saved two posts since the offshore rotation no longer had to be covered.
Other aspects of the field organisation also underwent major changes in the mid-1990s, including a shift from seven technical departments to three geographical units. These were:
- the Ekofisk operations unit for the Ekofisk Complex, Ekofisk 2/4 A, Ekofisk 2/4 B plus K, and the H7 and B11 compression platforms
- the Ekofisk operations unit for Eldfisk and Embla (2/7 A plus FTP, 2/7 D and 2/7 B)
- the operations unit for the outlying satellites – 1/6 A, 2/4 D, 2/4 E (Tor), 7/11 A (Cod), 2/7 C (Edda) and 2/4 F (Albuskjell).
Each of these installations still had their own offshore installation manager (OIM) and the platform organisation was fairly similar to before, but with better coordination between drilling and production.
The various operations units each had operations and technical managers, maintenance organisation, own budget and cost control, and section for manning analysis.
While the operations units were cut from three to one in 1995, Phillips reverted the next year to the old model with three geographical areas which each had their own technical manager.
That illustrates the inconstant nature of the GEA’s organisational structure. Revisions have been made to meet new requirements as and when they arose.
The transition to Ekofisk II involved phasing out 10 platforms in addition to three which were no longer in operation (Albuskjell 2/4 F and booster platforms 36/22 A and 37/4 A).
Cod 7/11 A was shut down in 1997, while Albuskjell 1/6 A, West Ekofisk 2/4 D, Edda 2/7 C, Ekofisk 2/4 G, Ekofisk 2/4 P, Ekofisk 2/4 R, the Ekofisk tank and the northern flare stack followed in 1998.
Although two new installations – Ekofisk 2/4 X and Ekofisk 2/4 J – were to be brought on stream, part of the workforce would thereby become redundant.
As a result, much attention was devoted by the management to downsizing the company. The goal was to trim personnel on land and offshore by 20 per cent.
Such reductions were an international trend in all the oil companies during the late 1990s because of low crude prices and weaker earnings. A wave of mergers washed over the industry.
So the downsizing process which began around 1992 in Phillips ended up continuing throughout the decade and reduced the workforce from about 2 600 at its 1990 peak to 1 600 in 2002.
In the latter year, Conoco merged with Phillips to form a single company. That created challenges for the new Norwegian organisation headed by CEO Lars A Takla.
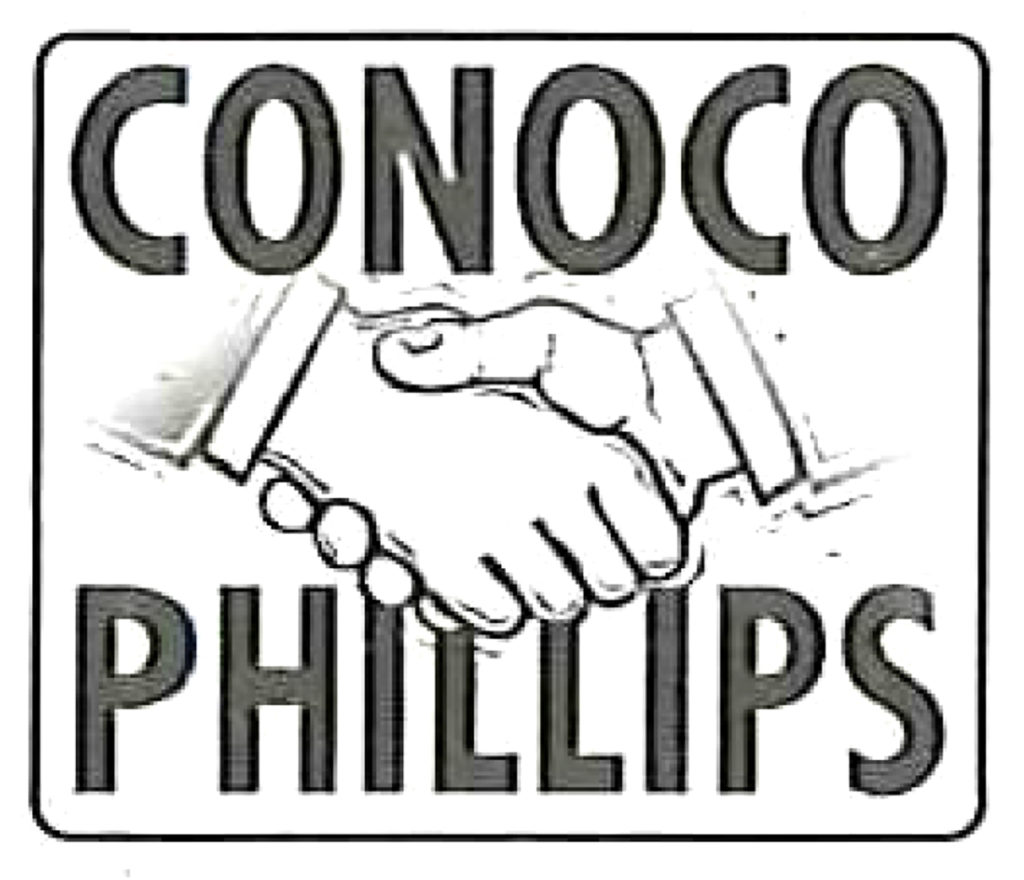
“Our first challenge in ConocoPhillips is to integrate the personnel from each company and create something better than the sum of Phillips and Conoco, so that we achieve a synergy,” Takla said in 2002.
“Although both companies hail from Oklahoma, and we possess more or less the same base values, we’ve had very different ways of doing things. So the way we work, take decision and so on therefore varies considerably.
“Phillips has had an operative role in Norway, while Conoco hasn’t. It’s never been in the production phase here, while the attention devoted to this in Phillips, with such extensive operations, has been very considerable.
“A lot happens on Ekofisk over a 24-hour period. Problems must constantly be dealt with, so you get this rush. One challenge, as I see it, is to get everyone to feel they’re playing in the same team rather than coming from two former outfits.”
The other challenge identified by Takla was that the union raised expectations of synergies such as increased revenues and reduced costs.
“One anticipation in all such mergers is that money will be saved,” he pointed out. “If you don’t live up to this, and fail to boost revenue or increase savings for one reason or another, that’ll have a negative effect on the share price.
“Joining forces provided a greater degree of independence. Both Conoco and Phillips were medium-sized, so we faced a threat that one of the majors would gobble us up. That created a genuine feeling of uncertainty among employees.
“Merging gave us the security of being big enough now. After all, this was a ‘merger between equals’. Together, we’d be a company which offered a future for our employees.
“But there’ll be great pressure over the next couple of years to deliver synergies and reduce costs. That can naturally have an impact on the size of the workforce.”
He noted that Phillips was very large in Norway and Conoco very small, but that the position was the exact opposite in the UK, for example.
“Although we have virtually no overlap, expectations exist about the synergies we’re going to achieve. It’ll be my job to ensure that we take the necessary steps to deliver these.
“That can be achieved by making us collectively a better company which delivers what the outside world expects of us, and by achieving a position relative to our portfolio of licences which makes us more balanced than before.
“We have production from Ekofisk and we’re the second largest licensee in Heidrun with 24.29 per cent in 2003 after [state-owned] Petoro.”
Takla pointed out that Heidrun ranked at the time as one of the biggest producing fields off mid-Norway, where Phillips had not had production activities before.
“We also have 14 per cent of Statfjord, which is important despite declining output from this field. Our joint revenues in Norway are up by about 70 per cent compared with Phillips alone.
“We’re now the biggest foreign operator on the Norwegian continental shelf. A number of years ago, Phillips ranked as the biggest taxpayer in Norway. We’ve since been surpassed by Hydro, Statoil and TotalFinaElf [now Total], but we’re still among the top four-five.”
He emphasised that Ekofisk was the main foundation, and said it was interesting that the first field to be discovered still had the largest remaining reserves.
“We have two jewels in our North Sea crown – Ekofisk and Treasure Britannia, a big gas field in the UK sector. What’s good about Ekofisk is that it’s a huge reservoir but takes a long time to produce because of low permeability.
“Our production licence for the field runs until 2028, but I think many factors indicate – when technological progress is taken into account – that we could perhaps produce until 2050.[REMOVE]Fotnote: Kvendseth, Stig S, Giant Discovery. A History of Ekofisk Through the First 20 Years, 1988: 193 (Phillips organisation chart); comments from Egil Lima and interview with Lars A Takla.