First well permanently plugged

Norwegian oil production began on the Ekofisk field in 1971, initially with trial output from four subsea wells – the original wildcat and three appraisals – tied back to the Gulftide rig. So bringing the very first well drilled on the NCS from a fixed platform into production in April 1974, just under three years later, was a major milestone.
A-13 was spudded (as the start to well drilling is known) in November 1973. This operation lasted for 163 days, and reached a total length of 3 444 metres. The first oil produced from the 2/4 A installation was piped on 25 April 1974 to loading buoy number one and on into shuttle tanker Elisabeth Fernstrøm. That marked the start of oil output from fixed platforms on the NCS. The well produced 82.2 million barrels of oil equivalent before finally shutting down after 39 years on 1 September 2013.
The actual plugging operation in 2016 took just under a month and was conducted by the Rowan Gorilla VI drilling rig. It involved setting five cement plugs at different levels in the well before it was permanently abandoned.
Because of its special history, the Xmas tree – set of valves – which sat on A-13 has been donated to the Norwegian Petroleum Museum and represents a unique object in its collection.[REMOVE]Fotnote: Pioner,2016.
Summer 2016: Record set for plugging operations
The largest annual number of permanent pluggings in the Greater Ekofisk Area (GEA) was achieved in 2016, when this job was conducted on 22 wells. Located on Ekofisk 2/4 A and 2/4 B as well as Eldfisk 2/7 A and 2/7 B, these wells witnessed the introduction and further development of new plugging techniques. That contributed to a substantial enhancement in efficiency, while major improvements were also implemented for rig operation.
“A well we recently plugged on Ekofisk 2/4 A was the 100th in the GEA since work on permanently plugging shut-in wells began in the late 1990s,” reported decommissioning manager Tim Croucher. Forecasts indicate that around 100 more wells are to be treated in the same way over the next 15 years. Croucher was particularly pleased at how efficiently the organisation managed to do this work, particularly on 2/4 A.[REMOVE]Fotnote: Pioner, no3, 2016. It took half the expected time, which meant reduced costs.
Well operations manager Wenche Wergeland, responsible for plugging with Rowan Gorilla VI on 2/4 A, was also satisfied and reported that the work had become more efficient. “We’re approaching 20 days per well,” she said. “That’s pretty impressive, given that our plans assumed 58 days when we started the plugging operations.”
How wells are plugged
In line with official requirements, primary and secondary plugs were set against the hydrocarbon-bearing formations, as well as a surface plug. That meant a total of five on 2/4 A – two against the reservoir and two against a formation higher up as well as the surface barrier.
Each plug was 55 metres (165 feet) long and formed from a special plugging cement. It had to extend to the well walls – in other words, from inside the casing right out to the formation.
Each well being plugged had to be logged to obtain data on its condition before the operation began. The most suitable method was determined on the basis of the logging results. One approach involves milling – a time-consuming operation to remove the metal from the steel casing used to line each well.
Where the casing was tight against the well wall, the formation itself could be used as a barrier, with the casing perforated at the top and bottom of the section to be plugged. A packer was then installed between the perforated areas and the flow between casing and well wall tested. If it was sealed, a cement plug could simply be positioned in the casing. Normally, the plugs were not completely tight and some throughflow was experienced. That was dealt with by a perforation, wash and cement (PWC) job. This meant that the area between casing and well wall was cleaned before setting the cement plug and anchoring it in the rock sides.
Conducting several jobs each time the equipment was run into the well saved time, since the running operation usually takes eight to 18 hours to implement. Before the well could be abandoned, a tight seal had to be confirmed. The plug was therefore checked by hacking at its top (tagging) and a pressure test conducted.
According to Wergeland, it paid to systematise experience by documenting all volumes used for the plug and taking cement samples to determine its strength. That cut the number of runs per well and thereby reduced rig time and costs.[REMOVE]Fotnote: Pioner, no2, 2016.
“A skilful commitment by our engineers on land as well as the operations team offshore has cut costs substantially from our original estimates and budgets for 2016,” Croucher told the Pioner house journal.
“That also makes it possible to reduce future removal budgets, which will make a noticeable contribution to the company’s initiative for cost reductions.”[REMOVE]
Fotnote: Pioner nr. 3, 2016.
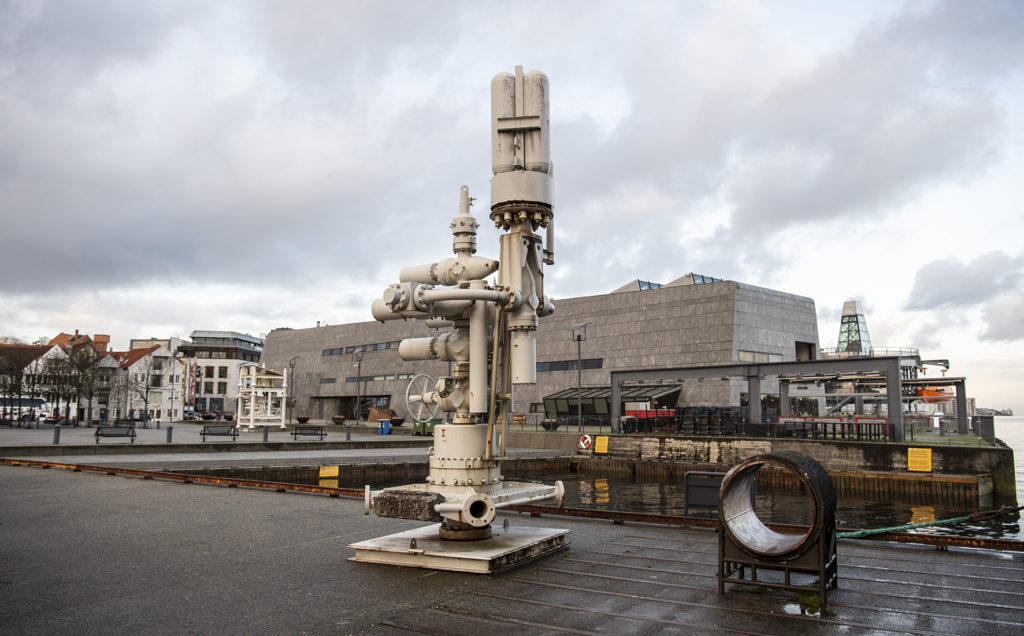